Операций за рабочими местами
З 4
З
Из рис. 5.3 видно, что продолжительность цикла изготовления партии деталей (п = З) на четырех операциях технологического процесса при 0следовательнопараллельном виде движения меньше, чем при последовательном на суммарное время совмещений т из-за того, что каждая пара смежных операций протекает параллельно. Число совмещений равно количеству операций в технологическом процессе за минусом единицы.
Время совмещения (параллельности) выполнения каждой пары смежных операций определяется по формуле
т = (п —Р)
где — наименьшее время выполнения операции, например, между первой и второй операциями, = между второй и Третьей операциями = 2, между тетьей и четвертой 4, = вэ
Суммарное время совмещений по всему технологическому
процессу рассчитывается по формуле
т-1 т-i
(п — р)в0 или (п — Р) 1КорI
i=1 i=i
Тогда продолжительность технологического цикла изготовления партии деталей при последовательно-параллельном виде
движения можно определить по формуле
‘п т-i
(пп) =п(, —(п —р)
1=1 1=1
Если на отдельных операциях обработка деталей ведется одновременно на нескольких рабочих местах (С), то
Т
(пп) п(п—р)—.
I=IСпр,, Ся,,
Подставив данные из приведенного выше примера, получим
продолжительность цикла обработки партии деталей при последовательно-параллельном виде движения
ТЦ() = 3 (2 + 1 + 1,5 + 2)— (3— 1)(1 + 1 + 1,5) = 12,5 мин.
При такой организации производственный цикл изготовления партии деталей характеризуется тем, что, во-первых, его продолжительность меньше, чем при последовательном вида движения, во-вторых, в нем отсутствуют перерывы в работе оборудования и рабочих, в-третьих, при этом виде движения общее время пролеживанця деталей на операциях намного меньше, чем при последовательном виде движения.
(5.5)
(5 6)
(5 7)
Время пролеживания одной детали на всех операциях технологического процесса определяется по формуле
= Тцщ1 — (5.9)
для рассматриваемого примера
= 12,5 — 6,5 = б мин.
Общее время пролеживания всех деталей в партии на всех операциях составляет
ТпвЗ 6=I8мин
Продолжительность производственного цикла при последоательно параллельном виде движения деталей по операциям определяется по формуле
Гт т—i 1
1ГП) =[п1(3 —(п —Р) корi +Т(0 +7 (5 10)
i=1 1=i см
Преимуществом этого вида движения является отсутствие перерывов в работе рабочих и оборудования и значительное сокращение продолжительности технологического (производственного) цикла по сравнению с последовательным видом движения. данный вид движения позволяет вести работу большими партиями и при большой трудоемкости изготовления деталей, благодаря чему он широко используется в серийном и крупносерийном производствах.
Сущность параллельного вида движения заключается в том, что детали передаются с одной операции на другую поштучно или транспортными партиями (р) сразу же после завершения обработки (независимо от времени выполнения смежных операций). При этом детали обрабатываются на всех операциях непрерывно и пролеживание их исключено. Это значительно сокращает продолжительность технологического цикла и, следовательно, производственного.
Пусть имеется такая же партия деталей, что и при последовательном и видах движения, и величина транспортной партии р = 1.
(5.8)
При построении графика параллельного вида движения партии деталей по операциям (рис. 5.4) необходимо соблюдать следующие правила.
1. Сначала построить технологический цикл для первой транспортной партии по всем операциям без пролеживания между ними.
2. На операции с наибольшей продолжительностью построить операционный цикл обработки деталей по всей партии (п) без перерывов в работе оборудования.
3. Для всех остальных транспортных партий достроить операционные циклы.
Тц(пар) = 10,5
Рис. 5.4. График продолжительности технологического цикла при параллельном движении деталей по операциям
Из рис. 5.4 видно, что продолжительность технологического цикла изготовления партии деталей (п = 3) на четырех операциях и при передаче их транспортными партиями (р = 1) определяется по формуле
или
т
(пар) пегiiах + — Р’яiах (5.11)
i=1
р”
(пар) (п—р)г’глах +р(,. (5.12)
1=1
Если на отдельных операциях работа выполняется одновременно на нескольких рабочих местах (С), то формула принимает следующий вид:
т._(‚тах
Ц(пар) —п—р—,—-—+Р —я———. (5.13)
‘‚-пр!
Подставив данные из приведенного выше примера, получим продолжительность технол’гического цикла при параллельном виде движения
Тц(пар)(3—1) 2 + 1 (2 + 1 + 1,5 +2) = 10,5мин.
Из графика и расчета видно, что технологический цикл изготовления партии деталей при данном виде движения является самым коротким по сравнению с другими видами движения. Вместе с тем на всех операциях, кроме максимальной по продолжительности, работа осуществляется с перерывами в работе оборудования за исключением случая, когда периоды выполнения операций технологического процесса равны либо кратны, т.е. сиихронньт. Этот вариант, называемый поточньтм видом движения, применяется при организации непрерывнопоточных линий.
Однако и при параллельном виде движения партии деталей по операциям технологического процесса детали пролеживают, во-первых, до начала обработки на первой операции и после Окончания обработки на последней операции и, во-вторых, внутри транспортной партии. При этом общее время пролеживания каждой детали в партии определяется по формуле
1пр Тц(пар)1о6р (5.14)
Для рассматриваемого примера
10,5—6,5 4 мин.
Общее время пролеживания всех деталей в партии составляет З 4 12 мин.
1 2,3
ж
ф
о
о.
ф
I
3-
4
О
П(тах
1 1 1 1
12345
1 1 I1 1
6 7 8 9 10 11 12 14 (,мин
1, 1 1, 1 1 1 1 II 1, 1
| 1 2 I 1 12 1 i
| 3 i 1 1 ‘3 1 2 3
|
Продолжительность производственного цикла при параллельном виде движения деталей по операциям технологического процесса определяется по формуле
г
х(iар) [(п_Р)гйiах +рЁ, +Т(у.д (5.15)
i=1
Преимущество этого вида движения состоит в том, что он обеспечивает наименьшую продолжительность технологического цикла и особенно, если процесс синхронизированный, а также равномерную загрузку рабочих и оборудования и высокую производительность труда. данный вид движения применяется в серийном и массово-поточном производствах.
53. Расчет и анализ продолжительности
производственного цикла сложного процесса
Производственный цикл сложного (сборочного) процесса представляет собой общую продолжительность комплекса координированньих во времени простых процессов, входящих в сложный процесс изготовления изделия или его партий. В условиях машиностроительного (радиоэлектронного) производства наиболее характерным примером сложного процесса является процесс создания машины, телевизора, металлорежущего станка или узлов, блоков, мелких сборочных единиц, из которых они состоят.
Производственный цикл сложного процесса включает производственные циклы изготовления всех деталей, сборку всех сборочных единиц, генеральную сборку изделия, контроль, регулировку и отладку. Построение сложного производственного процесса во времени осуществляется для того, чтобы определить продолжительность производственного цикла, скоординировать выполнение отдельных простых процессов, получить необходимую информацию для оперативно-календарного планирования и расчета опережения запуска-выпуска предметов труда. Целью координации производственных процессов, составляющих сложный процесс, является обеспечение комплектности и бесперебойности хода производства при полной загрузке оборудования, рабочих мест и рабочих.
Структура производственного цикла сложного процесса определяется составом операций и связей между ними. Состав операций зависит от номенклатуры деталей, сборочных единиц и технологических процессов их изготовления. Взаимосвязь операций и процессов обусловливается веерной схемой сборки изделия и технологией его изготовления. Предположим, что необходимо рассчитать продолжительность производственного цикла сборки изделия «А» (рис. 5.5).
Изделие
г ________
Блоки АА АБ АВ
(узлы) 7, 8 4, 5, 6 3
АВ1 АВ2
2 1
Рис. 5.5. Веерная схема сборки изделия «А>
Веерная схема сборки изделия показывает, какие узлы, подузльт, мелкие сборочные единицы можно изготавливать параллельно независимо друг от друга, а какие — только последовательно.
Технологический процесс и нормы времени выполнения операций по сборке изделия «А» приведены в гр. 1—5 табл. 5.1 (гр. 6—8 заполняются в процессе расчета). Месячная программа выпуска ‘Ув = 700 шт. Число рабочих дней в месяце Е = 21, режим работы участка $ = 2 смены. Потери рабочего времени на переналадку и плановые ремонты — 2% номинального фонда времени.
Так как изделия на сборку запускаются партиями, то прежде чем приступить к расчету продолжительности производственного цикла, необходимо определить следующие календарно- плановые нормативы: размер партии изделий; удобопланируемый ритм; количество партий, запускаемых в течение планового периода; время операционного цикла партии изделий; продолжи-
Сборочные
единицы
57
тельность операционного цикла партии изделий по сборочным единицам; число рабочих мест, необходимых для изготовления изделий. Затем построить цикловой график сборки изделий без учета загрузки рабочих мест; закрепить операции за рабочими местами; составить стандарт-план сборки изделий; построить уточненный цикловой график с учетом загрузки рабочих мест и определить продолжительность производственного цикла и опережения запуска-выпуска по сборочньим единицам и деталям.
Технологический процесс сборки изделия «А
Таблица 5.1
При решении вопроса о размерах партии необходимо исходить из экономически оптимальной величины.
Работа большими партиями позволяет реализовать принципы партионности, что обеспечивает: а) возможность применения более производительного процесса, что снижает затраты на изготовление изделий; б) сокращение ОдготовительнозаК71Ючитель- ного времени, приходящегося на единицу продукции; в) уменьшение потерь времени рабочихсборЩиков на освоение приемов работы (приноравливание к работе); г) упрощение календарного планирования производства.
Эти факторы способствуют росту производительности труда рабочих и снижению себестоимости продукции.
Однако в единичном и серийном производствах, где за каждым рабочим местом закрепляется выполнение нескольких операций и где преобладает последовательный вид движения предметов труда, с ростом размера партии повышается степень нарушения принципа непрерывности, поскольку каждая сборочная единица пролежi1вает больше времени, т.е. увеличиваются продолжительность производственного цикла изготовления партии изделий и число сборочных единиц, находящихся в заделе и на хранении (незавершенное производство). Кроме того, возрастает потребность в площадях для хранения изделий и в материальных ценностях, одновременно необходимых для производства.
Эти противоположные факторы, связанные с реализацией одного принципа (партионности) и нарушением другого принципа (непрерывности), с увеличением партии изделий требуют такого размера партии, при котором сочетание экономии от реализации первого принципа и потерь от нарушения второго было бы наиболее рациональным с экономической точки зрения. Этот размер партии принято называть экономIчески Оптимальным.
Определение оптимального размера партии изделий является одним из важнейших календарно-плановых нормативов при организации серийного производства, так как все остальные календарно-плановые нормативы устанавливаются на партию предметов труда.
Для расчета оптимального размера партий изделий разные авторы предлагают различные формулы, основанные на сопоставлении экономии и потерь. Однако из-за большой трудоемкости расчетов эти формулы не получили широкого применения. На заводах обычно используют упрощенный метод расчета исходя из приемлемого коэффициента потерь рабочего времени на гiереналадку и текущий ремонт рабочих мест (о.05). Как правило, вели-
59
Условное обозначение сбороч- ной единицы
| Номер опера- ции (i)
| Штуч- ное время на опе- рацию (1), мин
| Подго- тони- тельно- заклю- читель- ное время мин
| Подача сбороч- ной едини- цы к опс- рации
| Размер партии. изделии (IЧ) шт.
| Продолжительност операционног цикла
|
партии изделий
| партии по сборочной единице
|
|
|
|
|
|
|
|
|
АВ1
|
| 7, 0
|
|
|
|
|
|
АВ2
|
| 16,5
|
|
|
|
|
|
АВ
|
| 4,7
|
|
|
|
|
|
АБ
| 4 5 6
| 15,9 12,4 4,7
| 30 20 10
| 5 6 10
| 100 100 100
| 27 21 8
|
|
АА
| 7 8
| 7,0 16,6
| 20 20
| 8 9
| 100 100
| 12 28
|
|
А
| 9 10 11
| 11,3 7,6 9,5
| 10 20 10
| 11 11 —
| 100 100 100
| 19 13 16
|
|
Итого
|
| 113,2
|
| —
| —
|
|
|
чину этого коэффициента принимают от 0,02 для крупносерийного до 0,1 для мелкосерийного и единичного производств (или от 2 до 10 %). Если для определенных производственных условий задаться величиной данного коэффициента, то можно определить число изделий в партии по формуле
(100—сб)3,
а06
i=1
Полученный результат рассматривается как минимальная величина партии изделий. За максимальную величину можно принять месячную программу выпуска изделий (сборочных единиц).
Подставив данные из приведенного выше примера, получим
(I002).2008б. Л’ Л’ —700
— 2. 13 2 — ШТ., гОах — в — ШТ.
Таким образом, в результате проведенных расчетов устанавливаем пределы нормального размера партии изделий:
Л’0110 Л’гаах.
Предельные размеры партии изделий корректируются исходя из минимального размера. Корректировка начинается с установления удобопланируемого ритма (I?) — периода чередования партий изделий. Если в месяце 20 рабочих дней, то удобопланируемьими ритмами будут 20, 10, 5, 4, 2 и 1; если в месяце 21 день, то такими ритмами будут 21, 7, 3 и 1; если 22 дня, то 22, 11, 2 и 1.
Период чередования партий изделий (ритм) рассчитывается по формуле
— ________
гдеВ — число рабочихднейвмесяце,
— месячная программа изготовлеьо4я изделий, шт
Исходя из данных приведенного выше примера получим
21.86 =2,58 дня.
700
— (,ЛТ 60
7.100 + 20
1пиi= =12ч.
60
(5.16)
Если по расчету получается дробное число, то из ряда удобопланируемых ритмов выбирают ближайшее целое число, т. е. принятое значение периода чередования (]?).
Из удобопланируемых ритмов 21, 7, 3 и 1 выбираем ближайшее значение = З дня.
Далее в соответствии с принятым периодом чередования корректируем размер партии изделий по формуле
Н =1? -=3 =100шт. (5.18)
Н ПР]) 21
Выполняется условие 86 100 < 700.
Нормальный размер партии изделий должен быть кратным месячной программе выпуска (запуска) изделий.
Число партий в месяце () определяем по формуле
IЧ, 700
Х=—=—=7партии. (5.19)
ЛТ 100
Результат расчета оптимального размера партии изделий за- носим в гр. б табл. 5.1.
Продолжительность операционного цикла партии изделий по каждой операции (Ё рассчитывается по формуле
_________ (5.20)
Для сборочной единицы на первой операции (см. табл. 5.1)
(5.17)
Аналогично выполняем расчеты по другим операциям и результаты вписываем в гр. 7 табл. 5.1.
Продолжительность операционного цикла партии изделий по сборочньгм единицам определяется по формуле
1сбед = 1Пи,, (5.21)
1=1
где ‘с — число операций, входящих в сборочную единицу.
Для сборочной единицы АБ (см. табл. 5.1)
о
ю
о
о
о
= 27 + 21 + 8 = 56 ч.
Аналогично выполняем расчеты по другим сборочным единицам и результаты вписываем в гр. 8 табл. 5.1.
Необходимое число рабочих мест для сборки изделий рассчитывается по формуле
(пи,
С=’. (5.22)
для рассматриваемого примера:
92
С =4места.
Р 328
Необходимая численность рабочих определяется по формуле
(5.23)
где К, — коэффициент, учитываюIций списочную численность (можно
принять К = 1,1).
для рассматриваемого примера:
Ч 42 1,1 = 9 чел.
Построение щiклового графика сборки изделия «А». При построении такого графика не учитывается загрузка рабочих мест. Оно осуществляется на основе веерной схемы сборки (см. рис. 5.5) и продолжительности циклов сборки каждой операции и каждой сборочной единицы (см. табл. 5.1, гр. 7 и 8). Как правило, такой график строится в порядке, обратном ходу технологического процесса, начиная с последней операции (рис. 5.6, а), в зависимости от того, к какой операции поставляются сборочные единицы. Продолжительность цикла этого графика будет Минимальной. Однако условия производства и ограниченные ресурсы требуют выполнения определенных работ последовательно, на одном и том же рабочем месте или стенде. Все это приводит к изменению циклового графика и, как правило, к смещению запуска на более ранние сроки и следовательно, к увеличению продолжительности цикла.
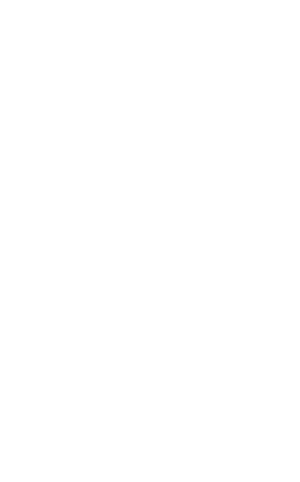
Для достижения равномерности загрузки рабочих мест и рабочих-сборщиков необходимо закрепить операции за рабочими местами. С этой целью на каждое рабочее место набирается объем работ, продолжительность операционного цикла которых не должна превышать пропускную способность рабочих мест на протяжении принятого периода чередования (iабл. 5.2).
Построение стандарт-плайа сборки изделия <А» (циклового графика с учетом загрузки рабочих мест). Этот график строится на основе циклового графика без учета загрузки рабочих мест (см. рис. 5.6, а) и данных табл. 5.2. При этом необходимо, чтобы продолжительность циклов отдельных операций графика проецировалась на соответствующие рабочие места на графике (рис. 5.6, 6). В таком случае сохраняется продолжительность производственного цикла на графике, построенном без учета загрузки рабочих мест (см. рис. 5.6, а).
Таблица 5.2
Однако не всегда удается это осуществить. В рассматриваемом примере сдвинуты сроки начала выполнения операций 4, 5, б и 1. Из-за сдвига работ на более раннее начало увеличилась продолжительность производственного цикла и сборочные единицы вынуждены были пролеживать какое-то время. На этом же графике (см. рис. 5.6, 6) необходимо изобразить производство второй, третьей и последующих партий изделий до тех пор, пока не заполнится один период чередования партий изделий. Заполнен- ный период чередования представляет собой стандарт-план, так
как именно здесь показаны стандартные, повторяюшиеся сроки проведения отдельных операций сборки каждым рабочим-сборiциком.
Построение уточненного циклового графика сборки изделия «А» и определение фактической продолжительности производственного цикла. Как правило, эта продолжительность несколько больше минимальной, так как выполнение некоторых операций сдвинуто на более ранние сроки.
Уточненный цикловой график сборки изделия «А» (рис. 5.6, в) строится на основе графиков, приведенных на рис. 5.6, а и 6, и по этому графику определяется фактическая продолжительность производственного цикла сборки партии изделий. В рассматриваемом примере эта величина составляет 96 ч. Волнистые линии на рис. 5.6, в показывают время смещения запуска соответствующих сборочных единиц АБ и АВ1.
Важным календарно-плановым нормативом является опережение запуска-выпуска сборочных единиц изделия «А». Расчет этого норматива ведется непосредственно на самих графиках в третьей и четвертой колонках на рис. 5.6, а и 5.6, в. В связи с необходимостью смещения запуска сборочных единиц АБ и АВ1 на более ранние сроки (см. рис. 5.6, в) изменилось и опережение запуска-выпуска этих сборочных единиц, а продолжительность производственного цикла стала на 8 ч больше, чем на первоначальном графике.
Если к цикловому графику сборки пристроить графики заготовки и обработки деталей (Г — Г12) (см. рис. 5.6, в), то можно получить график и длительность цикла изготовления изделия «А».
Глава б
ОРГАНИЗАЦИЯ ПРОИЗВОДСТВЕННОГО ПРОЦЕССА
В ПРОСТРАНСТВЕ
6.1. ПроизводствеНная структура предприятия
В соответствии с рассмотренным выше содержанием производственного процесса как совокупности основных, вспомогательных и обслуживающих процессов производственного назначения на любом машиностроительном (радиоэлектронного приборостЗакреплени
операций за рабочими местами
Номер рабочего места
| Номер операции, закреплен-. мои за рабочим местом
| Условное обозна- чение сборочной единицы
| Суммлрная продолжи- тельность операцион- ного цикла, ч
| Про- пускная способ- ность рабочего места за48ч
| Коэффициеят загрузки рабочего места
|
4 3 2 1
| 9,10,11 6,7,8 4,5 1,2,3
| А АА,АБ АБ АВ,АВ1, 2
| 48 48 48 48
| 48 48 48 48
| 1 1 1 1
|
роения) заводе различаются основные, вспомогательные и побочные цехи и обслуживающие хозяйства. Их состав, а также формы производственных связей между ними принято называть производственной структурой предприятия, которая является составной частью общей структуры предприятия (рис. 6.1).
Цех — организационно обособленное подразделение предприятия, состоящее из нескольких производственных и вспомогательных участков и обслуживающих звеньев. В нем выполняются определенные ограниченные производственные функции, обусловленные характером разделения и кооперации труда внутри предприятия. На большинстве промышленных предприятий цех является основной структурной единицей. Часть мелких и средних предприятий может быть построена по бесцеховой структуре. В этом случае предприятие делится непосредственно на производственные участки. Некоторые наиболее крупные предприятия в организационно-административном отношении строятся по корпусной системе, при которой несколько цехов и хозяйств объединяются под единым руководством.
К цехам основного производства относятся цехи, изготовляющие основную продукцию предприятия. Это заготовительные (литейные, кузнечно-прессовые и др.), обрабатывающие (механической обработки деталей, холодной штамповки, термические и др.), сборочные (узловой сборки, генеральной сборки, монтажные, регулировочно-настроечные и др.) цехи.
Вспомогательные цехи способствуют выпуску основной продукции, создавая условия для нормальной работы основных цехов: оснащают их инструментом и приспособлениями, обеспечивают запасными частями для ремонта оборудования и проводят плановые ремонты, обеспечивают энергетическими ресурсами. Важнейшими из этих цехов являются инструментальные, ремонтно-механические, ремонтно-энергетические, ремонтно-строительные, модельные, штамповочные и др. Число вспомогательных цехов и их размеры зависят от масштаба производства и состава основных цехов.
Побочные цехи — это такие, в которых изготавливают продукцию из отходов основного или вспомогательного производства либо восстанавливают использованные вспомогательные материалы для нужд производства, например цех производства товаров широкого потребления, цех регенерации формовочной смеси, масел и обтирочных материалов.
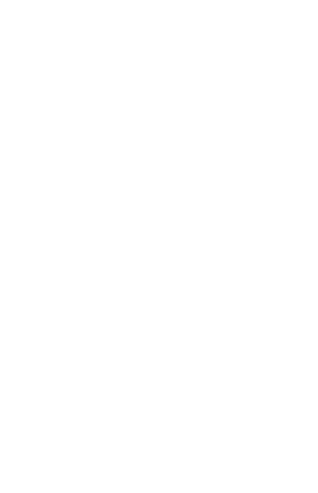
Подсобные цехи Осуществляют подготовку основных материаЛОВ ДЛЯ ОСнОВнЫХ цехов, а также изготовляют тару для упаковки продукции.
К обслуживающим хозяйствам производственного назначения относятся: складское хозяйство, включающее различные заводские склады и кладовые; транспортное хозяйство, в состав котороГО входят депо, гараж, ремонтные мастерские и необходимые транспортные и погрузочноразгрузочньте средства; санитарнотехническое хозяйство, объединяющее Водопроводньте, канализационные, вентиляционные и отопительные устройства; центральная заводская лаборатория, состоящая из механической, металлографической химической, пирометрической, рентгеновской и других лабораторий. Все они выполняют работы по обслуживанию основных, вспомогательных и побочных цехов.
Производственная структура включает общую структуру предприятия, в которую, кроме производственных цехов и обслуживающих хозяйств производственного назначения, входят различные общезаводские службы, а также Хозяйства и предприятия, связанные с капитальным строительством, охраной окружающей среды и культурно-бытовым обслуживанием работников, например жилищнокоммунальное хозяйство, подсобное хозяйство, столовые, профилактории, медицинские учреждения, детские ясли, клубы и т.п.
Производственная структура предприятия формируется при его создании, а также в результате непрерывно осуiцествляемого на нем в последующем процесса организации Она Определяется большой совокупностью факторов, ОСНоВНЬтМИ из которых являются конструктивные и технологические особенности производимой продукции; объемы выпуска по каждому виду продукции; формы специализации подразделений предприятия, формы кооперирования с другими предприятиями по выпуску конкретных видов продукции; нормативы численности и управляемости производственных подразделений и др.
Конструктивные особенности произво димой продукции и технологические методы ее изготовления во многом предопределяют состав и характер производстненньх процессов, видовой состав технологического оборудования, профессиональный состав рабочих, что в свою очередь обусловливает состав цехов и других производственных подразделений, а следовательно, и производственную структуру предприятия.
Объем выпуска продукции влияет на дифференциацию производСтвенной структуры и сложность внутрипроизводственных связей между цехами. Чем больше объем выпуска продукции, тем, как правило, крупнее цехи предприятия и тем уже их специализация.
Наряду с объемом решающее влияние на производственную структуру оказывает номенклатура продукции. Именно от нее зависит, должны ли цехи и участки быть приспособлены для производства строго определенной продукции или более разнообразной. Чем зже номенклатура продукции, тем относительно проще структура предприятия.
Формы специализации производственных подразделений определяют конкретный состав технологически и предметно специализированных цехов, участков предприятия, их размещение и производственные связи между ними, что является важнейшим фактором формирования производственной структуры.
Экономически целесообразные формы кооперирования пре дприятий по выпуску различных видов продукции позволяют реализовывать часть производственных процессов вне данного предприятия и тем самым не создавать на предприятии часть тех или иных цехов и участков или обслуживающих хозяйств.
Нормативы численности и управляемости производственных подразделений, определяемые количеством рабочих, занятых в цехах и на участках, существенно влияют на размеры предприятий, и, как следствие, на производственные структуры.
Производственная структура предприятия не может не изменяться в течение длительного времени, она динамична, так как на предприятиях всегда происходят: углубление общественного разделения труда, развитие техники и технологии, повышение уровня организации производства, развитие специализации и кооперирования, соединение науки и производства, улучшение обслуживания производственного коллектива. Все это вызывает необходимость ее совершенствования.
Структура предприятия должна обеспечивать наиболее правильное сочетание во времени и в пространстве всех звеньев производственного процесса.
Все многообразие производственных структур машиностроительных предприятий в зависимости от их специализации можно свести к следующим типам: заводы с полным технологическим циклом, располагающие совокупностью заготовительных, обра-
69
батывающих и сборочных цехов; заводы механосборочного типа (с неполным технологическим циклом), располагающие ограни - ченным числом основных цехов и, как правило, получающие необходимые заготовки в порядке кооперирования со стороны; заводы сборочного типа, выпускающие готовые изделия из деталей и комплектующих, изготовляемых на других предприятиях; заводы, специализирующиеся на производстве заготовок, как правило, построенные по принципу технологической специализации; заводы подетальной специализации, производящие отдельные детали, блоки, узльт, подузлы и сборочные единицы.
Производственная структура предприятия определяет разделение труда между его цехами и обслуживающими хозяйствами, т.е. внутризаводскую специализацию и кооперирование производства, а также предопределяет межзаводскую специализацию производства.
6.2. Формы специализации основных цехов предприятия
Основные цехи предприятий машиностроения, в которых производственные процессы проходят заготовительную, обрабатывающую и сборочную стадии, могут быть сгiециализированы в технологической, предметной или предметно-технологической форме.
Технологическая форма специализации в цехах предполагает выполнение определенной части технологического процесса, состоящей из нескольких однотипных операций при весьма гиирокой номенклатуре обрабатываемых деталей. При этом в цехах устанавливается однотипное оборудование, а иногда близкое по габаритам. Примером цехов технологической специализации могут служить литейные, кузнечные, термические, гальванические и др.; среди механообрабатьтвающих цехов — токарные, фрезерные, шлифовальные и др. В таких цехах, как правило, изготавливается вся номенклатура заготовок или деталей. Если же это сборочный цех, то в нем собираются все изделия, выпускаемые заводом (рис. 6.2).
Технологическая форма специализации цехов имеет свои преимущества и недостатки. При небольшом разнообразии операций и оборудования облегчается техническое руководство и создаются более широкие возможности регулирования загрузки оборудования, организации обмена опытом, применения рациональны
технологических методов производства. Эта форма специализации обеспечивает большую гибкость производства при освоении выпуска новых изделий и расширении изготавливаемой номенклатуры без существенного изменения уже применяемых оборудования и технологических процессов.
Рис. 6.2. Схема формирования цехов по технологическому принципу специализации
К существенным недостаткам можно отнести усложi-тение и удорожание внутризаводского кооперирования, ограничение ответственности руководителей подразделений за выполнение только определенной части производственного процесса.
При использовании технологической формы специализации в заготовительных и обрабатывающих цехах складываются сложные, удлиненные маршруты движения предметов труда с неоднократным их возвращением в одни и те же цехи. Это нарушает принцип прямоточности, затрудняет согласование работы цехов, приводит к увеличению производственного цикла и, как следствие, к росту незавершенного производства.
По технологическому принципу преимущественно формируются цехи на предприятиях единичного и мелкосерийного производств, выпускаюших разнообразную и неустойчивую номенклатуру изделий.
Литейный цех
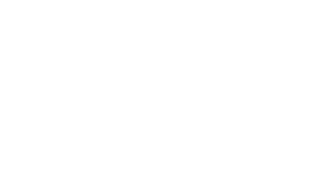
Предметная форма специализации цехов характерна для заводов узкой предметной специализации. В цехах полностью изготавливаются закрепленные за ними детали или изделия узкой номенклатуры, например одно изделие, несколько однородных изделий или конструктивно и технологически однородных деталеи (рис 6 3)
Рис. 6.3. Схема формирования цехов по предметному принципу специализации
В цехах с предметной формой специализации устанавливается разнообразное оборудование и оснастка, но выпускают они детали или изделия узкой номенклатуры Оборудование подбирается в соответствии с технологическим процессом и располагается в зависимости от последовательности выполняемых операций. Такое формирование цехов характерно для предприятий серийного и массового производств
Предметная форма специализации цехов, так же как и технологическая, имеет свои преимущества и недостатки, К первым можно отнести простое согласование работы цехов, так как все
операции по изготовлению конкретного изделия (детали) сосредоточены в одном цехе Все это приводит к устойчивой повторяемости производственного процесса, повышению ответственности руководителя цеха за выпуск продукции в установленные сроки, в определенном количестве и требуемого качества, к упрощению оперативнопроизводственного планирования, сокращению производственного цикла, уменьшению числа и разнообразия маршрутов движения предметов труда, сокращению потерь времени на переналадку оборудования, уменьшению межоперационного времени и ликвидации межцеховогО пролеживания, а также к созданию условий, благоприятных для внедрения поточных методов производства, комплексной механизации и автоматизации.
Опыт работы предприятий показывает, что при предметной форме ециализации цехов перечисленные выше преимущества приводят к повышению производительности труда рабочих и ритмичности производства, к снижению себестоимости продукции, росту прибыли и рентабельности и улучшению других технико эконох1ических показателей.
Однако эта форма специализации имеет и некоторые весьма существенные недостатки. Научнотехнический прогресс способствует расширению номенклатуры выпускаемой продукции и большему разнообразию применяемого оборудования, а при узкой предметной специализации цехи оказываются не в состоянии выпускать требуемую номенклатуру изделий без дорогостоящей их реконструкции.
Цехи, циализированные на выпуске ограниченной номенклатуры предметов труда, целесообразно создавать лишь при больших объемах их выпуска. Только в этом случае оборудование будет загружено полностью и переналадка его, связанная с переходом на выпуск другого объекта, не будет вызывать больших потерь времени. В таких цехах появляется возможность осуществлять замкнутый (законченный) цикл производства продукции. Эти цехи получили название предметнозамкнутых. В них иногда совмегцаются заготовительная и обрабатываюшая стадии или обрабатываюшая и сборочная (например, механосборочный цех).
Технологическая и предметная формы специализации в чистом виде используются довольно редко. Чаще всего на предприятиях машиностроения применяют смешанную (пре дметно-техяо’ логическую) специализацию, при которой заготовительные цехи строятся по технологической форме, а обрабатываюшие и сборочные объединяются в предметнозамкнутые цехи или участки.
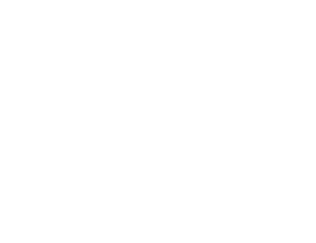
6.3. Производственная структура основных цехов предприятия
Под производственной структурой цеха понимают состав входящих в него производственных участков, вспомогательных и обслуживающих подразделений, а также связи между ними.
Эта структура определяет разделение труда между его подразделениями, т.е. внутрицеховую специализацию и кооперирование производства.
Производственный участок как объединенная по тем или иным признакам группа рабочих мест представляет собой структурную един
Воспользуйтесь поиском по сайту: