Химический и физико-химический контроль процесса.
Нормы технологического режима и метрологическое обеспечение.
Таблица 6
Наименова
ние стадий процесса, аппараты, показатели режима
| Номер пози
ции прибо
ра по схеме
| Единица измерения
| Допустимые пределы технологи
ческих параметров
| Требуемый класс точно
сти измери
тельных прибо
ров
| Примеча
ние
|
|
|
|
|
|
|
Аппарат Е1
1,4-бутандиол
а)температура
б)давлении
в)уровень
|
705,705а
503,503а
|
°С
кгс/см2
(МПа)
м³
|
25-30
0,2-0,5
0,02-0,05
0-4,0
|
1,0
3,5
1,5
|
|
Аппарат Е2
Толуиленди-
изоцианат
а)температура
б)давлении
в)уровень
|
809,809а
809б
504,504а504б
|
°С
кгс/см2
(МПа)
м³
|
25-40
0,2-0,5
0,02-0,05
0-8,0
|
1,0
2,5
1,0
|
|
Аппарат
Е3
полиэфир
а)температура
б)давление
|
7061-1У
706а1-1У
6091-1У
|
°С
кгс/см2 (МПа)
|
30-100
0,2-0,5
0,02-0,05
|
2,5
2,5
|
Термопара ТХК,вторичный прибор,электронный потенциометр КСП-4И.Предел измерения 0-150°С.
|
Реактор
Л1
1.Синтез СКУ-8М
- загрузка полиэфира
а)объем
б)температура
-сушка полиэфира
а)температура
б)давление вакуумметрическое
в)время
|
-
706в1-1У
7061-1У
706в1-1У
7061-1У
6111-1У
часы
|
л
°С
°С
кгс/см2
МПа
|
До 440,0
50-100
100±10
(-0,9)÷(-1,0) (-0,09) ÷(-0,1)
|
-
2,5
2,5
2,5
|
ТХК,
КСП-4И
ТХК,КСП-4И
ОБМВ-1-160
До массовой доли воды не более 0,05%
|
Охлаждение полиэфира
а)температура
б)давление
|
7061-1У
706в1-1У
6111-1У
|
°С
кгс/см2 (МПа)
|
60-70
(-0,9)÷(-1,0)
(-0,09)÷(-0,1)
|
2,5
2,5
|
ТХК,
КСП-4И
ОБМВ-1-160
|
Загрузка 1,4-бутандиола и катализатора
а)температура
б)время
в)объем
|
7061-1У
706в1-1У
часы
|
°С
ч
кг
|
60-80
0,5
8,77÷10,42
|
|
ТХК
КСП-4И
|
Ввод толуилендиизоцианата
а)температура
б)давление
в)время
г)объем
|
7061-1У
706в1-1У
6111-1У
часы
|
°С
кгс/см2
ч
л
|
55-80
0,2-0,25
53,29÷59,95
|
2,5
| Допускается кратковременный подъем температуры до 88°С
ОБМВ-1-162 от 0 до 6,0 кгс/см2
|
Разгрузка реактора Слив полимера в подготовленные противни
а)давление
б)время
|
6121-1У
часы
|
кгс/см2
мин.
|
1,0-3,0
20-30
|
2,5
|
ОБМВ-1-160 от 0 до 6,0 кгс/см2
|
Отверждение жидкого полиуретана в термостате Т1
а)температура
б)время
|
706а1-1У
7061-1У
часы
|
°С
ч
|
80-100
8-20
|
2,5
|
ТХК,КСП-4И от 0 до 150 °С
В случае неотверждения полимера в течение 20ч.при наличии свободных NCO групп допускается термостатирование до 40 ч.при тем.не более 100°С
|
Система трансформаторного масла
Аппарат № 170
уровень
|
501а,501
|
м³
|
0-3,2
|
| Уровень буйковый УБ-П
Вторичный прибор «Старт»
|
На линии теплообменника № 171
температура
|
801а,801б,801
|
°С
|
25-40
|
0,5
| Прибор КСП-4,регулирующий клапан ПКС-64-15-06
|
На линии нагнетания насоса № 1721-II
давление
|
601,602
|
кгс/см2 (МПа)
|
2,0-10,0
(0,2-1,0)
|
2,5
| Манометр ОБМ1-160,шкала от 0 до 10 кгс/см2
|
Система горячей воды аппарат 180
уровень
|
501,501а
|
мм
|
|
1,0
| Уровень буйковый УБ-ПВ,вторичный прибор МОШ1-160
|
Линия нагнетания насоса № 181
Давление
|
|
кгс/см2 (МПа)
|
2,0-6,0
0,2-0,6
|
2,5
| Манометр ОБМ-1-160
Шкала от 0 до 10 кгс/см2
|
Линия теплообменника № 182
температура
| 801,801а,801б
| °С
| 80±2
| 1,0
| Термометр сопротивления ТСП 5072А.Прибор КСМ-34.Регулирующий клапан ПКС-64-15-06
|
На линии пара в пароэжекционный вакуум-насос № 106
давление
|
802а,802
|
кгс/см2 (МПа)
|
4,0-6,0
0,4-0,6
|
0,6
| Показания,регулировка,регистрация
|
На линии ПЭУ № 106
давление
|
| кгс/см2 (МПа)
| (-0,9)÷(-1,0)
(-0,09)÷(-0,1)
| 2,5
| показание
|
Обратная вода из кондесаторов ПЭУ № 106,140
температура
|
709-712
|
°С
|
10-35
|
|
показание
|
Масса продукта
| Почтовые весы
|
|
|
| показание
|
Контроль технологического процесса.
Таблица 7
Наименование стадий процесса, анализируемый продукт
| Место отбора пробы (место установки средств измерения)
| Контролируе
мые показатели
| Методы контроля (методика анализа, ГОСТ или ОСТ)
| Норма
| Часто
та контроля
| Кто контро
лирует
|
|
|
|
|
|
|
|
Полиэфир П-6
| Из аппарата Е3
| Массовая доля гидроксильных групп,в % в пределах
Массовая доля воды, % не более
Активность, ч
| ТУ 38.103582-85
| 1,6-1,9
0,08
1-6
| Каждая партия
| Сырье
аяя лабора
торная ОТК
|
Толуилендиизоцианат Т-80\20
| Из тары поставщика
| Внешний вид
Массовая доля основного вещества в пересчете на толуилендиизоцианат, % не менее
| ТУ 113-03-12-17-85
| Прозразная жидкость без осадка
99,5
| Каждая партия
| Сырье
аяя лабора
торная ОТК
|
1,4-бутандиол
| Из тары поставщика
| Массовая доля 1,4-бутандиола, % не менее
| ТУ 64-5-65-86
| 98,0
| Каждая партия
| Сырье
аяя лабора
торная ОТК
|
Азот
| Из линии
| Массовая доля азота, % не более
| ГОСТ 9293-74 сорт 1,2
| 99,0
| По требованию
| Сырье
вя лабора
торная ОТК
|
Отверждение полимера
| Из противней в термостате
| Массовая доля изоцианатных групп
| Методика № 13
|
|
|
|
Готовый полимер
| Из тары
| Все показатели по:
ТУ38.103253-80
|
ТУ38.103253-80
|
|
|
|
Воздушная среда
| У аппарата
| Массовая доля толуилендиизоцианата
| По методике в сборнике Перегуд «Химический анализ воздуха промышленных предприятий»
|
| 3 раза в неделю
| Лаборатория ГСС
|
Сточные воды после ПЗУ
|
| Массовая доля изоцианата, ХПК, рН
| По методике № 15
По универсоальной индикаторной бумаге
|
| 1 раз в 10 дней
| Лаборатория ОТК при цехе 10
|
Характеристика и количество
Побочных продуктов и отходов производства
Твердые и жидкие отходы.
Таблица 8
Наименование отходов
| Куда складиру
ется
| Периодичность образования
| Условие (метод) и место захоронения, утилизации
| Кол- во т/год
| примечание
|
Полиэфир для промывки реактора Л1
| Складируется на площадке цеха с целью его дальнейшей переработке
| 1 раз в год
|
| 0,8
| |
Отработан
ое трасформа
торное масло
|
«»
| 1 раз в 2 года
| регенерация
| 0,5
| |
Сточные воды.
Сточными водами являются воды от охлаждения рубашки реактора Л1, конденсаторов ПЭУ № 106, паровой конденсат из рубашки реактора.
Таблица 9
Наименова
ние стока
| Кол-во образования сточных вод м 3 / час
| Условия (метод) ликвидации, обезвреживания, утилизации
| Периодичность выбросов
| Куда сбрасывается
| Установленная норма содержания загрязнений в стоках
|
Химически загрязненная вода
|
| Биологическая очистка
| 8 часов в сутки
| В канализацию хим.загрязненных стоков, кол.10-62
| ХПК не более 20, рН 6,5-8,0
|
Водный мыльно-содовый раствор
|
| «»
| 4 раза в год
| «»
| ХПК не более100, рН 6,5-9,0, мочевина не более 10 мг/л
|
Выбросы в атмосферу.
Таблица 10
Наименование выброса
| Кол-во образовавшихся выбросов по видам м 3 / час
| Условие (метод) ликвидации, обезвреживания, утилизации
| Периодичность выбросов
| Установленная норма содержаний и загрязнений в выбросах мг /м 3
| примечание
|
От вентус-уснановки
| 0,114 (изоцианаты)
|
| постоянно
| 0,5
|
|
В-283
В-286
| 0,324 (изоцианаты, ТДИ)
|
| постоянно
| 0,5
|
|
Технологические расчеты
9.1 Технологический расчет основного оборудования.
Размер аппарата определяется его производительностью:
Объем аппарата определяем по формуле
V=
3
Где g – производительность, кг/ч
tпреб. – время пребывания, ч
φ –коэффициент заполнения
ω – выход продукта с единицы объема
ω= w*ρ, где w=mпр. / mр.см.
mпр. – масса продукта, кг/ч
mр.см. – масса реакционной смеси, кг/ч
ρ – плотность реакционной смеси, кг/м3
w= 
ω = 0,92*1130,75=1040,29 кг/м3
V=
3
Принимаем аппарат объемом 1м3
Техническая характеристика.
1. Расчетное давление в аппарате
Или расчетное наружное давление
| 10 кгс/см2
7,0 кгс/см2
|
2. Расчетное давление в рубашке
| 6,0 кгс/см2
|
3. Расчетная температура в аппарате
| 100 ° С
|
4. Расчетная температура в рубашке
| 100 ° С
|
5. Рабочая среда в аппарате
| Агрессивная, пожароопасная, токсичная
|
6. Внутренний диаметр аппарата
| 1000 мм
|
7. Внутренний диаметр рубашки
| 1100 мм
|
8. Материал аппарата
| 12x18H10T
|
9. Материал рубашки
| Сталь В Сm3nc4
|
Примечание: допускается замена углеродистой стали на сталь с более высокими механическими свойствами, разрешенную «Правилами устройства и безопасной эксплуатации сосудов, работающих под давлением», без пересчета.
Исходные данные.
Таблица 11
№
| Наименование параметров
| Обозначение
| Величина
|
|
|
|
|
| Рабочее давление в корпусе
| Р
| вакуум
|
| Рабочее давление в рубашке
| Р
| 6 кгс/см 2
|
| Расчетное наружное давление на корпус
| Рн
| 7 кгс/см2 ,1 кгс/см2
|
| Расчетное внутренне давление в рубашке
| Рр
| 6 кгс/см 2
|
| Рабочая температура в корпусе
| t
| 150 ° C
|
| Рабочая температура в рубашке
| t´
| 200 ° C
|
| Расчетная температура в корпусе
| t
| 200 ° C
|
| Расчетная температура в рубашке
| t´
| 250 ° C
|
| Допускается напряжение при t=200 ° C для материала
Обечайки корпуса 12x18Н10Т
Днища корпуса 08x22Н6Т
|
[r]
[r] 1
|
1400 кгс/см 2
1930 кгс/см 2
|
| Допускаемое напряжение при t= 250 ° C для материала рубашки Всm3nc4
|
[r] 1
|
1200 кгс/см 2
|
| Модуль продольной упругости при t=200 ° C для материалов 12x18H10T
| E
| 1.97*106 кгс/см 2
|
| Коэффициент запаса устойчивости
| Пу
| 2,4
|
| Коэффициент прочности сварного шва
|
| 1,0
|
| Внутренний диаметр корпуса
| D
| 100 см
|
| Внутренний диаметр рубашки
| D´
| 110 cм
|
| Толщина стенки обечайки корпуса
| S
| 1,0 см
|
| Толщина стенки днища корпуса
| S1”/S 1
| 0,8/1,0 см
|
| Толщина стенки обечайки рубашки
| S 1
| 0,8 см
|
| Толщина стенки днища рубашки
| S 11
| 0,6 см
|
| Прибавка на коррозию
| с
| 0,2 см
|
| Длина обечайки корпуса по паспорту
| l
| 109 см
|
| Длина обечайки рубашки по паспорту
| l 1
| 975 см
|
9.2 Расчет количества оборудования.
Количество оборудования определяется по формуле:
n= Gt *t/g*tэфф.
Где Gt – производительность аппарата,кг/год
t- коэффициент запаса прочности (1,05÷1,2)
g – производительность, кг/ч
tэфф. – эффективный фонд времени работы установки, ч
g= 
n= 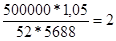
выбираем два реактора объемом 1 м3.
9.3 Механический расчет.
Расчет обечайки, нагруженной наружным давлением Pн = 7 кгс/см2
Допускаемое наружное давление
7.36 кгс/см2 > 7 кгс/см2
где допускаемое давление из условия прочности
кгс/см2
а допускаемое давление из условия устойчивости а пределах упругости:
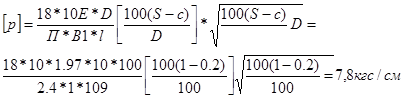
B1 = min 
Расчет эллиптического днища, нагруженного наружным давлением Pн = 7 кгс/см2
Допускаемое наружное давление:
кгс/см2 > 7 кгс/см2
где допускаемое давление из условий прочности:
кгс/см2
R=D
а допускаемое давление из условия устойчивости в пределах упругости
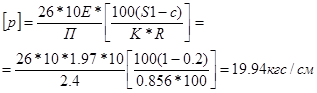
Кэ
Где x=10* 
H=0.25D=0.25*100=25 см.
Расчет мешалки.
Для перемешивания применяем лопастную мешалку
Диаметр мешалки равен:
dм=Dв/(1,4 ÷1,7),мм
где Dв-внутренний диаметр аппарата 
dм= 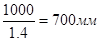
b=0.1dм
b=0.1*700=70мм
hм=(0,1 ÷0,3)dм
hм-расстояние от днища аппарата до мешалки,мм
hм=0,3*700=210мм
Стандартные параметры для лопастной мешалки dм=700мм
Скорость вращения:
ω=6,6 рад/сек
n=1,05сек-1
n=63,0 об/мин
Мощность =0,16 кВт
Расчет мощности:
Расчетная мощность Nм (Вт), потребляемая перемешивающим устройством собственно на перемешивание определяется по формуле:
Nм=κN*ρс*h3*dм5, Вт
где dм-диаметр мешалки, м
ρс-плотность перемешиваемой среды, кг/м3
h- частота вращения мешалки, об/сек
κN- критерий мощности
κN зависит от центробежного критерия Reц, отношение Dв/dм, типа перемешивающего устройства.
Центробежный критерий Reц
Reц=ρсhdм2/μс
где μс- динамический коэффициент вязкости смеси, H ּсек/м2
Reц=(1130,75*1,05*(0,7)2)/3000*10-6=2*105
κN=0,18
Nм=0,18*1130,75*(1,05)3*(0,7)5=39,6 Вт
Мощность, определяемая с учетом влияния внутренних устройств:
N=к1*к2*к3*Nм
N=1.3*1.2*1.1*39.6=68 Bт
Мощность двигателя:
Nдв= 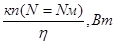
где
- КПД редуктора (
=0,93)
-коэффициент запаса (
=1,25)
Nдв= 
Выбирается электродвигатель типа ВАО-42-4 исполнение обычное с мощностью 3,0 кВт и числом оборотов 270 об/мин
Размеры мешалки:
dм=700 мм
d=45мм
b=70 мм
s=8 мм
m=6,3 кг
Мк*=84Hм
Мк*- наибольший крутящий момент при спусковой мощности.
Проверочный расчет вала.
Предварительный минимальный диаметр вала:
d= 1.71 3
, м
где М` к - расчетный крутящий момент на валу с перемешивающим устройством, Н*м
τ – допускаемое напряжение на кручение для материала вала. Для стали τ=44*106 Н/м2
М`к =
, Н*м
где N`м – расчетная мощность, расходуемая на перемешивание, Вт
ω – угловая скорость вращения перемешивающего устройства, рад/сек
М`к =
Н*м
d=1.71
м
Масса единицы длины сплошного вала:
m= 
где ρ – плотность материала вала, кг/м3 . Для стали ρ=7,85*103 кг/м3
m=7.85*103 
Определим момент инерции поперечного сечения вала:
y= 
y= 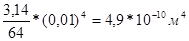
Определим коэффициенты к и а1:
к= 
а1= 
где Мм- масса перемешивающего устройства, кг
l1 и L – длина соответствующих участков вала
к= 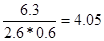
а1= 
По полученным значениям из графика на рис. находим корень L частного уравнения:
L= f(к,а1)= f(4,05;0,7)=1,4
Первую критическую скорость определяем по формуле:
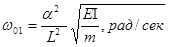
где L – расчетная длина вала, м
E- модуль упругости материала вала, Н/м2. Для стали E=2,2*1011 Н/м2.
ω01=
рад/сек
ω≤0,7 ω01
6,6<2.6
Условие не выполняется. Конструктивно диаметр вала принимаем 50 мм.
9.4 Тепловой расчет.
Расчет реактора:
1. Тепло, необходимое для нагрева самого реактора
Q1= σ ∙ Cc ∙ (t k - t н) = 1580∙0,12 (383-293)=17067 ккал
G=1580 кг – масса реактора
Cc = 0,12 ккал/кг С 0 – теплоемкость стали
t k= 383 К – конечная температура процесса
t н= 239 К – начальная температура процесса
2. Тепло, необходимое для нагрева реакционной массы:
Q2 = σП6 ∙ CП6 ∙ (t k - t н) + σТДИ ∙ CТДИ ∙ (t k - t н) + σ б/д∙ Cб/д ∙ (t k - t н)
σП6 = 390,285кг – масса полиэфира
σТДИ = 50,94 кг- масса ТДИ
σ б/д = 8,775 кг – масса 1,4 бутандиола
CП6 = 0,55 ккал/кг С0 – теплоемкость полиэфира
CТДИ =0,451 ккал/кг С0 – теплоемкость ТДИ
Cб/д = 0,48 ккал/кг С0 – теплоемкость ТДИ
t k= 373 К – конечная температура процесса
t н= 293 К – начальная температура процесса
Q2 =390,285*0,55(373-293)+50,94*0,451(373-293)+8,775*0,48(373-293)=10761,15 ккал
3.Тепло, выделяющееся в ходе поликонденсации:
Qвыд.=63*292,76=18443,88ккал
63 ккал – тепло, выделяющееся на 1 моль прореагировавшего ТДИ
292,76 моль – количество моль ТДИ (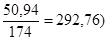
4.Общее количество тепла, затраченное на одну операцию:
Q1+ Q2 + Qвыд.= 17067+10761,15+18443,88=46272,03 ккал
5. Среднечасовой расход тепла:
Q = 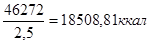
6. Градиент температуры
А=(tк – t гк)/ (tк – t гн)=(373-333)/(353-333)=2
∆Тср. =
С°
Находим необходимую поверхность рубашки:
Fруб.расч. =
2
Fреальное = 4 м2
3,81<4
Выполняется необходимое условие Fруб.расч <Fреальное
Воспользуйтесь поиском по сайту: