Магнитореологическая обработка
Традиционные методы финишной обработки высокоточных линз, керамики и полупроводниковых пластин являются очень дорогими и трудоемкими. Основным препятствием в изготовлении высококачественных точных линз является, как правило, то, что они изготовлены из хрупких материалов, таких как стекло, которое может треснуть во время обработки. Даже одна микротрещина может существенно снизить качество объектива и сделать его абсолютно непригодным для дальнейшего использования.
Обработку линз можно разделить на два этапа: шлифование и отделочная обработка. С помощью шлифования осуществляется получение линзы нужного размера, а в процессе отделочной обработки удаляются трещины и другие мелкие дефекты поверхности. Обычно производители осуществляют шлифование линз вручную, что делает этот процесс достаточно трудоемким. Возможно, основным недостатком ручного шлифования и отделочной обработки является то, что эти процессы не автоматизированы. Для преодоления этих трудностей Центром Производства Оптики (Рочестер, штат Нью-Йорк) была разработана технология для автоматизации отделочной обработки линз, известная как магнитореологическая обработка (МРО) [7].
Процесс МРО опирается на уникальные «умные» жидкости, известные как магнитореологические (МР) жидкости. МР-жидкости – это суспензии микронных размеров намагниченных частиц, таких как карбонильное железо, диспергированные в немагнитных средах, таких как силиконовое масло, миниральные масла, вода. В отсутствие магнитного поля идеальные МР-жидкости находятся в состоянии покоя. С применением внешнего магнитного поля наблюдается феномен, называемый Магнитореологическим эффектом (рисунок 7). На рисунке 7а представлено случайное распределение частиц в отсутствии внешнего магнитного поля; на рисунке 7б под воздействием магнитного поля частицы намагничиваются и выстраиваются в цепочки. Частицы приобретают дипольные моменты, пропорциональные напряженности магнитного поля. И когда дипольное взаимодействие между частицами превышает значение показателя их тепловой энергии, частицы выравниваются в цепочки диполей, которые ориентированны по направлению действия магнитного поля [8]. На рисунке 7в показано положение, приобретаемое частицами, в следствии действия напряженности магнитного поля и напряжений сдвига γ.
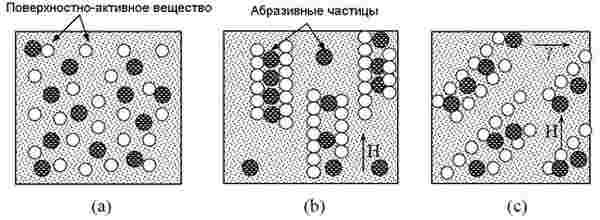
Рисунок 4 - Магнитореологический эффект
Реологически, поведение МР-жидкости под действием магнитного поля описывается пластической моделью Бингмана [9]:
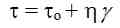
где τ – напряжения сдвига в жидкости, τ0 – напряжения сдвига, генерируемые действием магнитного поля; η – динамическая вязкость жидкости и γ' – интенсивность сдвига [ s-1 ].
Динамическая вязкость в основном зависит от типа жидкости. Величина τ0 зависит от напряженности магнитного поля, Н. Силы, действующие в жидкости (например напряжения сдвига), возрастают с увеличением сил магнитного поля. Однако это увеличение не является линейным, так как частицы являются ферромагнитными и значение показателя намагниченности различных частиц может колебаться [10]. Давление, создаваемое МР-жидкостями на поверхности линзы, могут варьироваться в пределах 50 – 100 кПа, для создания такого давления напряженность магнитного поля должна изменяться в диапазоне 150 - 250 кA/м (~2-3 kOe) [11]. Максимальная напряженность магнитного поля ограничена значением магнитной проницаемости МР-жидкости.
Благодаря возможности управления реологическими свойствами путем изменения силы тока, МР-жидкости получили широкое распространение в различных отраслях промышленности. МР-жидкости используются в амортизаторах и различных демпфирующих устройствах, муфтах, тормозах, приводах, также данные жидкости применяются при обработке эндопротезов [12]. Параметры обработки могут регулироваться путем изменения силы и направления магнитного поля, действующего на жидкость. Стандартные МР-жидкости эффективны для финишной обработки оптических стекол, керамики, пластмасс и некоторых немагнитных металлов [13].
Исходя из схемы процесса магнитореологической обработки, приведенной на рисунке 8, выпуклые, вогнутые или плоские заготовки помещаются над опорной поверхностью. Согласно рисунку 9, слой МР-жидкости расположен на внешней части вращающегося диска. Под воздействием магнитного поля в рабочем зазоре происходит ориентирование абразивных частиц в МР-жидкости и осуществляется формирование зоны обработки. Устранение микронеровностей и дефектов поверхности происходит благодаря повороту линзы в зоне обработки относительно своей оси с постоянной скоростью [14]. Удаление материала происходит за счет создания МР-жидкостью напряжений сдвига на обрабатываемой поверхности. Автоматизация отделочной обработки плоских, цилиндрических и шаровых поверхностей может быть осуществлена за счет контроля процесса обработки с помощью ЭВМ.
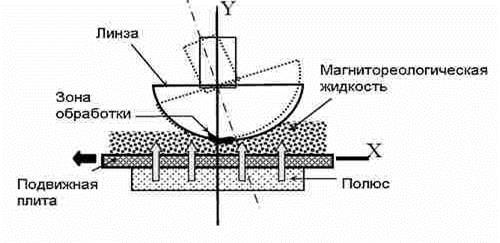
Рисунок 5 - Схема магнитореологической обработки
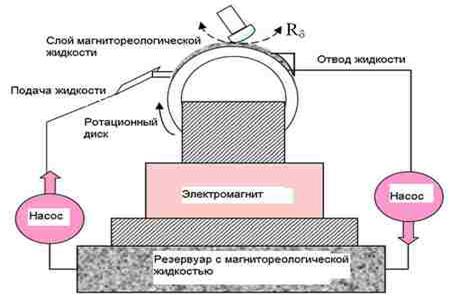
Рис. 6 - Вертикальная установка для магнитореологической обработки
Отделочная обработка поверхностей с помощью МР-жидкостей имеет ряд преимуществ по сравнению с традиционными методами финишной обработки:
1. силы резания регулируются с помощью магнитного поля;
2. жидкость удаляет тепло и стружку из зоны обработки;
3. силы, действующие на обрабатываемую поверхность, имеют значительно меньшие значения чем при шлифовании кругом;
4. МР-жидкость автоматически приспосабливается к форме обрабатываемой поверхности, копируя ее.
Управляемый с помощью ЭВМ, магнитореологический процесс позволил производить обработку поверхности с точностью 10 – 100 нм, и снял многие ограничения, присущие обычным видам финишной обработки [7]. Уникальные характеристики данного метода, сделали его наиболее эффективным при отделочной обработке оптики, входящей в состав приборов навигации, медицинского оборудования, военной техники (прибор ночного видения, инфракрасный бинокль и т. п.) и т. д.
Наношлифование
В наноразмерном масштабе (<100 нм), на первый взгляд, нет различия между полированием и шлифованием. Действительно, допустимая погрешность размера при наношлифовании соизмерима с допустимым значением шероховатости. Различие между нанополированием и наношлифованием заключается в том, что при нанополировании допустимая погрешность размеров не обязательно лежит в наноразмерном диапазоне. Тогда как целью наношлифования является не только снижение шероховатости, но и достижение суперпрецизионной точности размеров.
Достижение суперпрецизионной точности при наношлифовании требует суперпрецизионной точности базирования (позиционирования) обрабатываемой заготовки. В силу этого, многие технологические подходы, применяемые при нанополировании, оказываются неприменимыми для наношлифования. В частности, неприменимы технологии, связанные с напылением и распылением материала.
Монопольное положение среди всех методов наношлифования в настоящее время занимает обработка связанным абразивным материалом (кругами). До последнего времени обработка связанным абразивом применялась в основном для предварительных нанотехнологических операций. Однако в последние годы появились новые модели суперпрецизионного шлифовального оборудования для нанообработки.
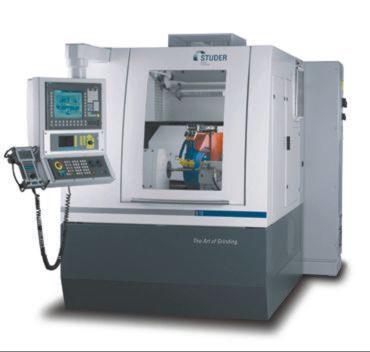
Рис.9.105 Cтанок модели Fritz Studer S12
В качестве примера можно привести круглошлифовальный станок модели S12 (рис. 9.105) фирмы Fritz Studer (Германия) для высокоэффективной обработки с погрешностью около 10 нм. Высокие точность и скорость обработки обеспечиваются за счёт новой комбинации привод/направляющие — линейные двигатели, которые обеспечивают скорость холостых перемещений до 30 м/мин при ускорении до 3 м/с2, а также за счёт уникальной станины из гранита с высокими демпфирующими свойствами. Термическая стабильность конструкции гарантировано сохраняется благодаря встроенным агрегатам охлаждения.
Также можно отметить ультрапрецизионные крупногабаритные профилешлифовальные станки UPG-DXNC (рис. 9.106) фирмы Okamoto (Япония). Станки оснащены гидростатическими направляющими. Давление масла в гидросистеме регулируется в зависимости от нагрузки на рабочий стол, что позволяет достичь прямолинейности продольного хода 0,5 мкм на 1000 мм и поперечного хода 0,4 мкм на 800 мм. Дискретность вертикальной подачи – 10 нм. Разрешающая способность линеек обратной связи – 2 нм. Зона шлифования – от 600×400 до 6000×800 мм.
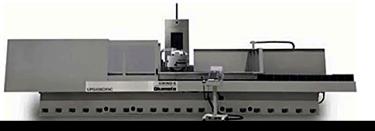
Рис. 9.106 Cтанок модели UPG-DXNC
Воспользуйтесь поиском по сайту: