Организация и обслуживание рабочих мест Рабочие места, их виды и требования к организации 7 глава
печении ими цехов и рабочих мест, в поддержании строгой конструкторской и технологической дисциплины.
Организация чертежного хозяйства основьтвается на ЕСК,д, которая предусматривает единые принципы классификации изделий и документации, ее индексацию, определенный порядок хранения, учета и дублирования документации, а также порядок внесения изменений.
Классификация и индексация чертежей и другой технической документации проводятся по объектам изготовления, стадиям конструкторской подготовки производства, целевому назначению и характеру использования.
По объекту изготовления выделяются чертежи изделий основного производства, чертежи изделий вспомогательного производства (инструмента, приспособлений, моделей, штампов и др.); технологические чертежи, изображающие поковки, штамповки и другие заготовки.
По стадиям конструкторской подготовки документы могут быть проектами, выполняемыми в процессе проработки многочисленных вариантов на разных стадиях проектирования, и рабочими чертежами, предназначенными для изготовления изделий, а также их эксплуатации. В соответствии с этим все конструкторские документы подразделяются на чертежи эскизного, технического и рабочего проектирования.
По целевому назначению и характеру использования все конструкторские документы подразделяются на оригиналы (авторские документы, выполненные на любом материале и предназначенные для изготовления подлинников), подлинники (документы, оформленные подлинными подписями и выполненные на материале, позволяющем воспроизведение копий), дубликаты (копии подлинников, обеспечивающие идентичность воспроизведения подлинника, позволяющие снятие с них копии), копии (документы, выполненные способом, обеспечивающим их идентичность подлиннику или дубликату, и предназначенные для непосредственного использования в производстве).
Для удобства учета и пользования всем чертежам присваивается индекс. Индексация чертежей — это условное обозначение, обычно цифровое. Как правило, используется единая обезличенная система индексации, основанная на десятичной классификации всех чертежей изделий и их частей (отО до 9). Все чертежи деталей, узлов, блоков, изделий делятся на 10 классов, классы — на
10 подклассов, подклассы — на 10 групп, группы — на 10 подгрупп, подгруппы — на виды деталей.
Индекс чертежа состоит из различительного индекса предприятия, классификационной характеристики изделия, порядкового регистрационного номера документа (в пределах организации-разработчика) и шифра документа (рис. 21.1).
Рис. 21.1. Индексация технической документации
Хранение, учет и дублирование чертежей и другой технической документации на заводе осуществляется в соответствии с «Правилами учета и хранения» в отделе технической документа- ции. В этот отдел входят: бюро подлинников и дубликатов (архив), где хранятся названные документы поформатно в порядке возрастания номеров и выдаются только для изготовления копий и дубликатов, внесения изменений и для восстановления при их износе; бюро копий, осуществляющее прием, регистрацию, выдачу, а также учет состояния и движения копий документов, учет применяемости документов; бюро внесения изменения в документацию, производящее изменения в конструкторской документации и учет внесения изменений; цех размножения документов, где размножаются, брошюруются и переплетаются конструкторские документы; бюро омплектации документов после их размножения.
Архивные документы (оригиналы) отражают первоначальное состояние конструкции после утверждения ее заказчиком; изменения в эту документацию не вносятся. Подлинники и дубликаты служат для справок и сверок, а также для изготовления копий.
ХХ
Т Шифр документа
Порядковый регистрационный номер документа (в пределах организацииразработчика)
ХХхХ ХХ Х Х Х Х ХХ)
Индекс организацииразработчика
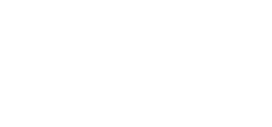
В них вносят изменения в установленном порядке, на руки их не выдают, пользуются ими только в помещении архива и бюро внесения изменений.
Порядок внесения изменений в конструкторскую документа- цию установлен ГОСТ 2.50344. Изменения в документацию имеет право вносить только организация — держатель оригиналов и подлинников на основе извещения об изменении, подписанного лицами, составившими и проверившими изменение, представителями технологического и стандартизационного контроля, представителями производственного отдела, представителем заказчика и лицом, утвердившим данное изменение. для уточнения вносимого изменения используют предварительное извещение, которое является документом временного пользования и погашается извещением на изменение, по которому вносится изменение в подлинник. Предварительное извещение утверждается главным инженером предприятия и визируется главным конструктором, главным технологом и начальником производства. Оно выпускается в случаях обнаружения в документе явной ошибки, которая может вызвать брак изделия, при необходимости предварительной проверки в производстве планируемого изменения и необходимости предварительной подготовки производства. При каждом изменении документу присваивается очередная литера.
21.4. Технико-экономическое обоснование
на стадии проектирования новой техники
Каждый вновь создаваемый вид техники или мероприятие по улучшению освоенной техники по сравнению с ранее освоенным должен давать большую экономию живого и овеществленного труда, быть лучше по качеству и в большей мере удовлетворять потребности в новых или усовершенствованных видах продукции. Показатели качества вновь создаваемой техники должны соответствовать уровню высших мировых достижений в данной отрасли.
Нозая или усовершенствованная техника должна быть лучше и эффективнее той, взамен которой она создается с производственной или эксплуатационной точки зрения.
В первом случае к новой (усовершенствованной) конструкции предъявляются требования как к объекту производства на заводе изготовителе. Главным здесь является экономичность производства и минимальные сроки его подготовки и освоения. Экономичность изготовления каждой новой конструкции зависит от ее технологичности, от того, насколько прогрессивными и производительными будут применяемые технологические процессы. Конструкция является технологичной, если она экономична для производства.
Выбор наилучшего варианта конструкции осуществляется по показателям технологичности, к которым относятся:
• трудоемкость изготовления — абсолютная (на одно изделие) и относительная (на единицу установленной мощности, производительности, другого показателя);
• материалоемкость или масса конструкции — абсолютная или относительная
• трудоемкость подготовки изделия к функционированию;
• степень конструктивной стандартизации и унификации;
• капиталовложения в производство новой продукции;
• себестоимость и отпускная цена новой продукции
• прибыль и рентабельность производства.
Трудоемкость изготовления продукнии определяется в процессе ее проектирования и является весьма важным показателем. Технологичнее считается та конструкция, которая при прочих равных условиях менее трудоемка. Задача снижения трудоемкости изделия на стадии его производства одна из важнейших, стоящих перед разработчиками. Большие возможности снижения трудоемкости заложены в правильном выборе современных прогрессивных Методов получения заготовок, рациональном выборе квалитетов и классов шероховатости. На смену обработке деталей резанием (механообработке) постепенно приходят точные методы формообразования деталей — штамповки, гiрессования, литья под давлением и др.
Материалоемкость характеризует общий расход материала на изготовление данной конструкции изделия или удельную материалоемкость на эксплутационный параметр. Во многих случаях конструктор имеет возможность выбрать при проектировании детали какой-нибудь один материал из двух или нескольких, обеспечивающих одинаковые эксплуатационные свойства детали, но различные по стоимости и трудоемкости обработки, а иногда способствующие снижению массы изделия.
Повышение определяющего эксплуатационного показателя изделия, как правило, приводит к снижению материалоемкости и трудоемкости в расчете на единицу основного параметра. При этом снижение удельной материалоемкости на единицу мощности или другого параметра происходит значительно быстрее, чем сокращение общего расхода материала на единицу изделия.
Трудоемкость подготовки изделия к функционированию определяется в процессе проектирования и зависит от сложности регулировочнонастроечнЫХ процессов, проводимых с целью получения необходимых техникоэкономическиХ параметров. Возможности снижения трудоемкости здесь заложены в качестве используемой контролЬноизмерительной аппаратуры и специальных стендов для испытаний.
Степень конструктивной стандартизации и унификации — это показатель, характеризующий конструкцию изделия с точки зрения реализации в ней стандартизированных и унифицированНЫХ деталей, что приводит к увеличению выпуска однотипных деталей, сборочных единиц, изделий в целом, а также применению более прогрессивной технологии, а это, как следствие, позволяет не только существенно снизить трудоемкость изготовления, но и несколько уменьшить материалоемкость.
Капиталовложения в производство новой конструкции характеризуют общие затраты на приобретение дополнительного и изготовление нестандартного оборудования и перепланировку в производственных цехах, создание производственных запасов. Чем меньше потребности предприятия в капиталовложениях, тем технологичнее новая конструкция изделия.
Себестоимость, прибыль и рентабельность новой конструкции изделия являются обобщающими показателями ее технологичности.
С производственной точки зрения новая конструкция будет считаться технологичной, а следовательно и эффективной в том случае, если дополнительная прибыль (\П), полученная в результате освоения, выпуска и реализации новой продукции, обеспечит рентабельность не ниже средней, сложившейся на предприятии-изготовителе рентабельности. Этому условию должно удовлетворять неравенство:
iП П
——— (21.1)
i\К Оф
где ЛК — дополнительные капиталовложения, связанные с освоением выпуска новой консТРукциИ
П — суммарная годовая прибыЛь предiIриятияизтовителя до освоения выпуска новой конструкЦиИ изделия;
Оф — стоимость производственных фондов предприятияизготови теля.
дополнительная прибыль, получаемая от реализаиии НОВОЙ
конструкции изделия, определяется ПО формуле:
АП = [IЧ2(Ц2 — С2) — — [Т41(Ц1 — С1)1, (21.2)
где ‚Ч1 и ‚Ч2 — среднегодовой выпуск ранее освоенной и новой КОI{СТруКХIИИ изделия соответственно;
iI и Ц2 — цены на ранее освоенную и новую конструкцию соответственно;
С1 и С2 — себестоимость ранее освоенной и новой конструкции соответственно;
— среднегодовые затраты, связанные с технической подготовкой и освоением в производстве конструкциИ нового изделия.
С 3сплуатациОННоЙ точки зрения потребителя, новая конструкция изделия должна быть: 1) более надежной в эксплуатации (долговечной безотказной, ремонтопригодной и сохраняемоЙ); 2) удобноЙ в обслуживании и ремонте, эстетичной и безопасноЙ в эксплуатации; З) эргономичноЙ (с точки зрения пСИХоЛОГИИ, физиологиИ и гигиены труда работников обслуживаНия) 4) более производительной в единицУ времени; 5) более экОНоМИЧНОЙ в потреблении электроэнергии и капиталовложений 3ГлуатационниКоВ НОВОЙ продукции. Кроме того, она должна обеспечивать минимальную себестоимость единицы работы, Выполняемой изделием.
Если 3луатациОНные свойства новой техники выше, чем у ранее освоенной (заменяемой), то экономическая эффективность ее определяется путем соизмерения капитальных вложений потребителя со снижением себестоимости работы, выполняемой новой техникой. Лучшим признается вариант с наименьшей суммой приведенных затрат:
и, + Е,К, —* тпiп, (21.3)
где И, — годовые эксплутационные издержкИ предприятия — потреби’ля продукции по i-му варианту;
367
К, — капитальные вложения предприятия — потребителя продукции по 1-му Варианту;
Е — нормативный коэффициент экономической эффективности
После расчета приведенных затрат по вариантам новой техники можно определитi годовой экономический эффект от использования новой или чсовершенствован ной техники.
Эксплутационная технологичность новой техники может быть определена с помощью нескольких показателей. При этом следует различать показатели технологичности базового и проектируемого изделий, а также определять уровень технологичности как соотношение показателей технологичности проектируемого и базового изделий.
Глава 22
ОРГАНИЗАЦИЯ ТЕХНОЛОГИЧЕСКОЙ ПОДГОТОВКИ
ПРОИЗВОДСТВА
22.1. Задачи и содержание технологической подготовки производства
Технологическая подготовка производства (ТПП) представляет собой совокупность мероприятий, обеспечивающих технологическую готовность производства, т.е. наличие на предприятии полных комплектов конструкторской и технологической документации и средств технологического оснащения, необходимых для выпуска заданного объема продукции с установленными технико-экономическими показателями. Это одна из важнейших стадий системы СОНТ, весьма значительная по объему и сложности. Так, трудоемкость технологической подготовкм по отношению к общей трудоемкости разработки технического проекта изделия в единичном производстве составляет 20—25%, в серийном — 50—55%, а в крупносерийном и массовом — 60—70%. Это связано с тем, что если двигаться от единичного производства к серийному и далее к массовому, то степень технологической оснащенности возрастает, а следовательно, увеличивается и объем работ по ТПП.
Технологическая подготовка производства на предприятии выполняется отделами главного технолога, главного металлурга, а также технологическими бюро основных цехов, в ведении которых находятся литейные, кузнечные, механические и сборочные цехи. Материальной базой для них служат инструментальный и модель- ный цехи, технологические лаборатории и опытное производство.
до начала работ по ТПП, как правило, проводится технологический контроль чертежей, который необходим для анализа и проверки запроектированных изделий (деталей) на технологичность их конструкций, правильность назначения классов точности обработки, рациональность схем сборки и т.д.
Основными этапами ТПП являются: 1) разработка технологических процессов; 2) проектирование технологической оснастки и нестандартного оборудования; З) изготовление средств технологического оснащения (оснастки и нестандартного оборудования); 4) выверка и отладка запроектированной технологии и изготовленного технологического оснащения.
На первом этапе осуществляются выбор рациональных способов изготовления деталей и сборочных единиц, разработка новых технологических процессов. Эта работа выполняется на основе:
чертежей на вновь спроектированное изделие; ГОСТов, отраслевых и заводских стандартов на материалы, инструмент, а также на допуски и припускв; справочников и нормативных таблиц для выбора режимов резанi4я; планируемых размеров выпуска изделий.
Содержание работ по проектированию технологических процессов складывается из следующих элементов: выбора вида заготовок; разработки межцеховых маршрутов; определения последовательности и содержания технологических операций; определения, выбора и заказа средств технологического оснащения установления порядка, методов и средств технического контроля качества; назначения и расчета режимов резания технического нормирования операций производственного процесса; определения профессий и квалификации исполнителей; организации производственных участков (поточных линий); формирования рабочей документации на технологические процессы в соответствии с ЕСТд.
На втором этапе ТПП, во-первых, проектируют конструкиии моделей, штампов, приспособлений, специаЛьного инструмента и нестандартного оборудования, а во-вторых, разрабатывают технологический процесс изготовления технологического оснаще368
ния, который должен быть достаточно универсальным, но в то же время прогрессивным, совершенным и обеспечивающим высокое качество изготовляемых деталей.
Разработка конструкций технологической оснастки осуществляется конструкторскими бюро по оснастке и инструменту в тесной взаимосвязи с технологами, которые проектируют технологические процессы обработки деталей нового изделия.
На третьем этапе ТПП изготавливают всю оснастку и нестандартное оборудование. Эта наиболее трудоемкая часть технологической подготовки (60—80% труда и средств от общего объема ТП П). Как правило, такие работы проводят постепенно, вначале ограничиваются минимально необходимой оснасткой первой необходимости, а затем повышают степень оснащенности и механизации производственного процесса до максимальных экономически оправданных пределов. На этом этапе осуществляют перепланировку (если это необходимо) действующего, монтаж и опробование нового и нестандартного оборудования и оснастки, поточных линий и участков обработки и сборки изделий.
На четвертом этапе ТПП выверяют и отлаживают запроектированную технологию, окончательно отрабатывают детали и узлы (блоки) на технологичность; выверяют пригодность и рациональность спроектированной оснастки и нестандартного оборудования, удобство разборки и сборки изделия; устанавливают правильную последовательность выполнения этих работ; проводят хронометраж механообрабатывающих и сборочных операций и окончательно оформляют всю технологическую документацию.
Технологическая документация для различных типов производства (единичного, серийного и массового) отличается глубиной разработки технологических процессов и степенью их детализации. Сначала разрабатывают маршрутные межцеховые карты на технологические процессы изготовления деталей и сборочных единиц. В маршрутньих картах указываются госледовательность прохождения заготовок, деталей или сборочных единиц по цехам и производственным участкам предприятия. Для изготовления деталей и сборки изделия в единичном или мелкосерийном производствах достаточно иметь конструкторскую документацию, маршрутное или маршрутно-операционное описание технологического процесса либо перечень полного состава технологических операций без указания переходов и технологических режимов.
для серийного и массового производств кроме маршрутнОЙ технологии разрабатывается технологический процесс с операционным описанием формообразования, обработки и сборки. При этом для единичных технологических процессов разрабатывается операционная технологическал карта, для типовых (груiiповых) технологических процессов — карта типовой (групповой) операции. В них указываются все переходы по конкретной операции и способы выполнения каждого, технологические режимы, данные о средствах технологического оснащения, материалах и затратах труда. Обычно в операционных картах помешают эскизньие чертежи, изображающие детали или части деталей и содержаIдие размеры и указания на обработку, необходимые для выполнения данной операции (способ закрепления деталей на станке, расположение инструмента, приспособления и т. д.).
Кроме того, для определенных изделий разрабатываются карты типовых технологических процессов нанесения электролити ческих покрытий, химической обработки, нанесения лакокрасочных покрытий, ведомостi1 удельных норм расхода растворите- лей, анодов, химикатов, ведомости подетальных отходов и другие документы.
Исходная информация для разработки технологических процессов может быть базовой, руководящей и справочной. Базовая информация включает наименование объекта, а также данные, содержащиеся в конструкторской документации. руководяЩ информация — это отраслевые и заводские стандарты, устанавливающие требования к технологическим процессам, оборудованию, оснастке, документация на действующие типовые и групповые технологические процессы, производственные инструкдии, документация для выбора нормативов, по технике безопасности и промышленной санитарии. Справочная информация включает документацию опытного производства, описание прогрессивных методов изготовления, каталоги, справочники, альбомы компоновок, планировок и др.
22.2. 0рСнизационноэконоМические пути
ускорения технологической подготовки производство
Одним из важнейших направлений сокращения трудоемкости и продолжительности ТПП является использование технологической унификации и стандартизации. К основным ее направлени370
ям относятся: типизация и нормализация технологических процессов; унификация технологической документации; групповые методы обработки деталей; унификация оборудования и технологической оснастки.
Под типиза цией техно4огическах процессов (ТТП) понимается система их рациональной разработки, основанной на создании групп конструктивно-технологически подобных деталей или сборочньих единиц. Наибольшее распространение ТТП получила при разработке технологических процессов механообработки.
ТТП обеспечивает: упорядочение существующей технологии; внедрение прогрессивных методов обработки и сборки; использование высокопроизводительной, быстропереналаживаемой оснастки и оборудования; применение принципов поточного производства в организации производственных процессов серийного и мелкосерийного производств; внедрение гибкого автоматизированного производства; значительное снижение трудоемкости разработки технологических процессов, а вместе с тем и сокращение сроков ТТП.
Работы по ТТП осуществляются в два этапа.
Первый этап — классификация деталей по группам конструктивно-технологического подобия и выбор типового представителя каждой группы. Подбор деталей в такие группы осуществляется по следующим признакам: близкие по конструктивному оформлению при одинаковых требованиях к точности и чистоте обработки поверхностей, одинаковой последовательности операций и однотипном использовании оборудования и оснастки.
Формирование таких групп, как правило, осуществляется на основе разработанного конструктивно-технологического класси - фикатора деталей, при котором детали предварительно группируются в классы по признаку служебного назначения, классы делятся на подклассы по конструктивным формам деталей, что обусловливает подобие их технологических маршрутов и идентичность применяемой оснастки. Дальнейшее разделение на группы (по признаку общности материала) обеспечивает унификацию технологического маршрута их обработки. И, наконец, все детали гругiпируются по типам в соответствии с требованиями точности ихЪбработки. Из каждой типовой группы деталей выбирается конкретная деталь, имеющая наибольшее число обрабатываемых поверхностей и наибольшую трудоемкость изготовления. Эта деталь принимается в качестве базовой для разработки технологии.
Второй этап — разработка технологического процесса на базовую деталь, который утверждается как типовой для данной группы. Кроме необходимых сведений для изготовления базовой детали ПП содержит указание о методах обработки всех деталей данной группы в виде полного перечня и последовательности операций и переходов обработки деталей данного типа.
При составлении технологического процесса для какой-либо новой детали прежде всего устанавливается, к какому типу и к какой группе она относится. Этим сразу определяется содержание технологического процесса, что значительно ускоряет его разработку и позволяет установить оптимальные режимы, так как последние уже отработаны на типовом процессе. Использование ТТП предъявляет более жесткие требования к технологичности деталей, а следовательно, заставляет конструкторов тщательнее подходить к их конструктивным формам.
ТТП сборки осуществляется с помощью типовых технологических схем, определяющих структуру технологического процесса в виде перечня типовых операций и последовательности их выполнения.
Нормализация технологических процессов (НТП) дополняет ТТП. В распоряжении технологов имеются технологические нормали на используемые исходные материалы (сплавы, марки, прОфили и др.), режимы и методы обработки (плавки, заливки, пагрева под ковку, штамповку, термообработку), геометрические элементы конструкций (радиусы закруглений, углы и т. д.), при- пуски, допуски, уклоны на штамповке и т. п.
Групповые методы обработки деталей аналогично ТТП базируются на классификации деталей по группам по тем же признакам конструктивнотехнологического подобия. Однако групповой технологический процесс разрабатывается не на конкретную базовую деталь, а на комплексную деталь, в которую включены все элементарные поверхности деталей, входящих в группу. Обработка данной группы деталей осуществляется с помощью групповой оснастки станка, настроенной на изготовление комплексной детали.
Унификация технологической документа ции приводит к сокращению общего количества документов, облегчению труда технологов при подготовке производства и внесении изменений в действующие процессы. К числу основных унифицированных документов, используемых при разработке ТТП, относятся карты
ТИПОВЫХ представителей, операционные технологические карты, сводные карты ТТП, операционные карты групповой обработки, сводные карты групповых процессов.
Унификация оборудования и технологической оснастки позволяет использовать ее при смеНе объектов производства, повысить коэффициент загрузки оснастки и ее эффективность, при этом можно вести обработку деталей большими партиями. Стандартизация оснастки существенно уменьшает затраты времени и средств на ее проектирование, сокращает цикл ее изготовления, является предпосылкой Специализации производства, что приводит к сокращению затрат на оснащение.
Наибольшее распространение на предприятиях получили такие системы унифицированной оснастки, как сборно-разборные, универсально-сборные, универсально-наладочные приспособления, универсальная безналадочная, неразборная специальная, специализированная наладочная.
Сборно-разборная оснастка (СРО) состоит из стандартных фиксирующих, зажимных, крепежных и специальных деталей; при перекомпоновке на новое изделие возможна доработка стандартных элементов. СРО представляет собой обратимую специальную оснастку долгосрочного применения. Она используется для обработки одной или нескольких деталей, а также пригодна для условий крупносерийного производства.
Универсально-сборная оснастка (УСО) собирается из стандартных деталей и узлов многократного использования, изготовлеiiньтх с высокой степенью точности. Используется для сверлильньтх, гокарных, фрезерных, расточньюх, шлифовальных, сварочных, штамповочных и других операций. Компоновки УСО после обработки данной партии деталей разбираются, детали и узлы используются для сборки других приспособлений и повторных компоновок. Недостатком этого вида оснастки являются высокая стоимость набора компоновочных элементов и пониженная жесткость приспособлений. Применяется преимущественно на заводах опытного, единичного мелкосерийного и серийного производств.
универсально-наладочные приспособления (УНП) имеют базовую оригинальную деталь и сменные наладки. Базовая деталь используется многократно, а сменные элементы предприятия изготовляют в соответствии с конфигурацией обрабатываемых деталей. Примером УНП являются универсально-наладочные тиски, патрон со сменными кулачками. К недостаткам УНП можис
отнести замену СМенНых наладок раньше их полного износа в связи с обычно возникающей необходимостью переходить на выпуск новых изделий. Применяются УНП в соответствии с классификацией обрабатываемых деталей и с внедрением ТТП.
универсальная безналадочная оснастка (УБО) используется для многократной и долговременной установки различных по форме и размерам заготовок, обрабатываемых на универсальных еталлорежуших станках. Преимущества этой оснастки — небольшие сроки и затраты на проектирование и изготовление, разнообразие деталей, для которых они могут применяться, возможность использовать их до полного износа. Основным недостатком УБО является невысокая производительность из-за необходимости постоянно выверять точность установки заготовок.
Неразборная специальная оснастка (НСО) долгосрочного применения используется, как правило, для одной деталеоперации в кругюносерийном и массовом производствах. К достоинствам НСО МОЖНО отнести высокую производительность так как не требуется выверять детали, размеры получаются автоматически, Обеспечивается высокое качество. Ее недостатки — большие сроки и стоимость проектирования и изготовления, невозможность использования при смене изделий, т.е. ухудшение гибкости производства.
циализированНая наладочная оснастка (СНО) используется для деталей, близких по конструктивнОтехнологичеСким признакам, имеющих общие базовые поверхности и одинаковый характер обработки. Эта оснастка состоит из базового агрегата и наладки. Она допускает регулирование элементов или замену специальной наладки. В этом случае детали обрабатываются по единому групповоМУ или типовому технологическому процессу.
другим важным направлением сокращения трудоемкости и продолжительности ТПП является создание и использование автоматизированных систем технологической подготовки производства (АСТПП), включающих системы томатизироваНного проектирования технологических процессов (САПРТП), системы матизированного проектирования технологического оснащения (САПРТО), системы автоматизированного проектирования производственных подразделений (САПРОП) и Системы 0матизированного управления технологической подготовкой производства (АСУТПП). Методика разработки и использования томатизированных систем данного направления приведена в работе [111.
375
Воспользуйтесь поиском по сайту: