Расчет межоперационньих оборотных заделов 2 глава
/1
480 ИЛИ(Ц]=—2—7;Д6].
1106]
Периодичность (ритм) партии изделий ]-го наименования в соответствии с выбранной партией деталей рассчитывается по формуле (8 50).
Продолжитсльность производственного цикла (заI-iятость МППЛ обработкой партии предметов труда]-го наименования) определяется по одной из формул
(8.60)
После определения календарно-плановых нормативов первой и второй групп составляют стандарт-план МППЛ с последовательно-партионным чередованием изделий у-го наименования и стандарт-планы по изготовлению каждого изделия, когда МППЛ работает как ОППЛ, а также строят эпюрьг движения оборотных заделов по каждому изделию, рассчитывают средние значения оборотных заделов, нсзаверiлснного производства и продолжительности производственного цикла обработки партии деталей за период оборота линии.
Стандарт-план МпПЛ с последовательно-партионным чередованием строится аналогично стандарт-плану МНПЛ.
Кроме того, необходимо построить т графиков стандарт-планов ОППЛ на период оборота линии, так как когда обрабатывается одно изделие л-го наименования, МППЛ работает как ОППЛ. другими словами, необходимо построить графики работы линии, графики регламентации труда, рассчитать межоперационные оборотные заделы изделий по каждому наименованию. Если т З, то графики стандарт-планов строятся по всем наименованиям изделий, а если т > 3, то графики строятся только для ведущих изделий не более трех наименований. Методика построения графиков стандарт-плана по каждому изделию аналогична методике построения стандарт-плана для ОППЛ.
8.8. Экономическая эффективность
поточного производство
Широкое распространение поточных методов производства объясняется их высокой эффективностью. для поточного производства характерны широкое применение высокопроизводительного специального оборудования, высокий уровень механизации и
автоматизации ручных работ и транспортных операций и наиболее полное использование оборудования, материалов и прочих средств производства
Эффективность поточных методов выражается в повышении производительности труда, увеличении выпуска продукции, сокращении продолжительности производственного цикла обработки продукцв, пiижение использования производственных площадей, меньшем числе межцеховых и цеховых кладовых, экономии материалов и снижении себестоимости продукции.
На повышение производительности труда при поточном производстве оказывает влияние несколько факторов, из которых можно отметить следующие:
• освобождение рабочих от затрат излишнего и тяжелого физического труда. Доставка на рабочие места материалов и полуфабрикатов, а также дальнейшее перемещение предметов труда осуществляются с помощью специальных транспортных средств;
• ликвидация или сведение к минимуму простоев рабочих из- за лереналадок оборудования, неравномерной загрузки, непропорциональности мощностей рабочих мест;
• приобретение рабочими производственных навыков вследствие того, что они в течение длительного времени выполняют одну и ту же операцию или ее часть;
• повышение точности заготовок и материалов, в результате чего сокращается время на обработку и изготовление продукции;
• снижение трудоемкости процессов производства за счет применения в потоке передовой технологии и техники и оптимальных режимов работы оборудования.
На снижение себестоимости влияют следующие факторы:
• сокращение заработной платы на единицу изделия благодаря повышению производительности труда и снижению трудоемкости продукции;
• уменьшение затрат на основные материалы и полуфабрикаты в результате рационального выбора этих материалов, установление более экономичных размеров и допусков материалов и припусков на полуфабрикатьт, применение наиболее эффективных методов централизованного метода раскроя с учетом максимального использования отходов производства;
• сокращение удельных расходов инструментов благодаря применению техники обоснованных типов и размеров инструментов, оптимальных скоростей, установленных режимов работы
Оборудования, организации принудительной смены и централизованной заточки;
• Экономное расходование в результате интенсификации процессов и увеличение выпуска продукции;
• наиболее полное использование оборудования, зданий и сооружений благодаря Целесообразной планировке оборудования, непрерывности и равномерности процессов производства, пропорциональности Мощностей и сЁедению простоев оборудования к Минимуму;
• сокращение брака в результате тщательной разработки технологического процесса, постоянства применения Материалов и режимов работы, освоения рабочими технологических процессов.
Внедрение поточного производства приводит к значительному сокращению продолжительности производственного цикла, уменьшению заделов и общего объема незавершенного производства.
Однако переход на поточное производство влечет за собой и рост капитальных Вложений. В связи с этим необходимо определять размер капитальных вложений и ИХ Экономический Эффект.
Расчет Экономического Эффекта рекомендуется вести в следующей последовательности
1. Выбор и обоснование базового варианта для сравнения.
2. Определение производительности техники по Вариантам.
3. Расчет капитальных Вложений по вариантам (базовому и проектируемому): К1 — до Внедрения поточного производства и К2 — после внедрения.
В общий объем капитальных вложений по вариантам, как правило, включаются: затраты на технологическое оборудование (К06), дорогостоящий инструмент и технологическую оснастку (Ка); затраты на доставку, монтажи пусконаладочные работы технологического оборудования и оснастки (К па); затраты на производственную площадь, занимаемую оборудованием (К); затраты на транспортные средства (К); затраты на предотвращение загрязнения окружающей среды (К) и на создание определенных условий для рабочих-операторов (К).
Кроме того, в состав капитальных вложений по проектируемому варианту (К2) включаются: затраты на научно-исследова тельские и опытно-конструкторские работы (Кб) с учетом фактора времени; убытки от списания недоамортизированной
базовой техники (Ка); затраты на пополнение (уменьшение) оборотных средств (ЬО).
4. Расчет себестоимости выпускаемой продукции по вариантам: производимой с помощью оборудования базового варианта (С1) и с помощью поточной линии (С2);
5. Установление тождественности объемов выпуска по базовому и проектируемому вариантам.
6. Определение суммы приведенных затрат и годового экономического эффекта от внедрения поточного производства (методика расчета изложена в разд. 9.6).
Глава 9
ОРГАНИЗАЦИЯ АВТОМАТИЗИРОВАННОГО
ПРОИЗВОДСТВА
9.1. Этапы развития автоматизации производства
Автоматизация производства — это процесс, при котором функции по управлению производством и контролю за ним, ранее выполнявшиеся человеком, передаются приборам и автоматическим устройствам. Автоматизация — это основа развития современной промышленности, генеральное направление научно-технического прогресса. Цель автоматизации производства заключается в повышении эффективности труда, улучшении качества выпускаемой продукции, в создании условий для оптимального использования всех ресурсов производства. Различают частичную, комплексную и полную автоматизацию производства.
При частичной автоматизации часть функций по управлению производством автоматизирована, а часть выполняется рабочими-операторами (полуавтоматические комплексьТ). Как правило, такая автоматизация осуществляется в тех случаях, когда управление процессами из-за их сложности или скоротечности практически недостугiно человеку
Комплексная автоматизация — это когда все функции по управлению автоматизированы, рабочие-операторы только налаживают технику и контролируют ее работу (автоматические комплексы). При комплексной автоматизации должна применяться такая система машин, оборудования и вспомогательной
техники, при которых процесс превращения исходного материала В ГОТОВЫЙ ПРОдУКТ происходил без физического вмешательства человека.
Полная автоматизация производства — высшая ступень автоматизации, которая предусматривает передачу всех функций управления и контроля комплексно-аВтоматизироВанным производством автоматическим системам управления.
Развитие автоматизации производства можно условно подразделить на три этапа.
Первый этап автоматизации охватывает период с начала)(УШ до конца ХIХ столетия. В 20-е годы ХУIII в. в России А. Т. Нартовым был разработан автоматический суппорт для токарно-копировального станка. В 1765 г. русский механик И.И. Ползунов, создатель первой паровой машины универсального назначения, впервые в мире разработал промышленный автоматический регулятор для поддержания постоянного уровня воды в котле паровой машины. В регуляторе Ползунова была реализована идея, являющаяся и поныне центральной в устройствах автоматического регулирования. В 1784 г. английский механик Дж. Уап разработал центробежный регулятор скорости для паровой машины.
В течение всего ХIХ столетия совершенствовалось устройство регуляторов для паровых машин. На первом этапе развития автоматизации были предприняты попытки создать автоматические станки и линии с жесткой кянематической связью. В этот период развитие автоматизации производства основывалось на принципах и методах классической механики.
Второй этап развития автоматизации производства охватывает период с конца ХIХ в. до середины ХХ в. Этот этап связан с развитием электротехникм и практическим использованием электричества в средствах автоматизации. В частности, важное значение имели изобретение П.Л. Шиллингом магнитоэлектрического реле (1850 г) — одного из основных элементов электроавтоматики, разработка Ф.М. Балюкевичем и другими в 80-х годах ХIХ в. устройств автоматической сигнализации на железнодорожном транспорте, создание С.Н. Алостоловым-Бердичевским и его соратниками первой в мире автоматической телефонной станции.
К началу ХХ в. относится широкое развитие и использование электрических систем автоматического регулирования. Индиви-
дуальный привод отдельных рабочих органов машин и введение между ними электрических связей существенно упростили кинематику маший, сделали их менее громоздкими и более надежными. Будучи более гибкими и удобными в эксплуатации, электрические связи позволили создать комбинированное электрическое и механическое программное управление, обеспечивающее автоматическое выполнение неизмеримо более сложных операций, чем на машинах-автоматах с механическим программным устройством. для второго этапа развития автоматизации характерно появление электронно-программного управления, в частности, были созданы станки с числовым программным управлением (ЧПУ), обрабатывающие центры и автоматические линии, содержащие в качестве компонента оборудование с программным управлением.
В 40—50-е годы ХХ столетия началось быстрое развитие радио- электроники. Электронные устройства обеспечивают наибольшее быстродействие, чувствительность, точность и надежность автоматических систем. Наступил третий этап развития автоматизации с широким использованием управляющих ЭВМ, которые для каждого момента рассчитывают оптимальные режимы технологического процесса и вырабатывают управляющие команды по всем автоматизируемым операциям.
Переходом к третьему этапу развития автоматизации послужили новые возможности ЧПУ, основанные на применении микропроцессорной техники, что позволило создать принципиально новую систему машин, в которой сочетались большая производительность автоматических линий с требованиями гибкости производственного процесса. Современные микроэлектроника и ЭВМ позволяют достигнуть высшего уровня автоматизации.
9.2. Организационнотехнические особенности создания и эксплуатации автоматических линий
дальнейшим развитием поточного производства является его автоматизация, в которой сочетаются непрерывность производственных процессов с автоматическим выполнением. Автоматизация производства в машиностроении и радиоэлектронном приборостроении развивается в направлении создания автоматических станков и агрегатов, автоматизированных и автоматических поточных линий, автоматизированных и автоматических участков, цехов и даже заводов.
Автоматическая линия — это система согласованно работающих и автоматически управляемых станков (агрегатов), транспортных средств и контрольных механизмов, размещенных по ходу технологического процесса, с помощью которых обрабатываются детали или собираются изделия по заранее заданному технологическому процессу в строго определенное время (такт автоматической линии).
Роль рабочего на такой линии сводится лишь к наблюдению за ее работой, к наладке и подналадке отдельных механизмов, а иногда к подаче заготовки на первую операцию и снятию готового изделия на последней операции. Это позволяет рабочему управлять большим числом машин и механизмов.
Автоматизация поточного производства аналогична развитию автоматизации производства и осуществлялась в три этапа.
Основным параметром (нормативом) автоматической линии является производительность. Ее величину считают по производительности последнего выпускного станка. Различают: технологическую, цикловую, фактическую и потенциальную производительность линии.
Технологическая производительность определяется по фор-
муле
рТ=1пм, (9.1)
где (,, — машинное время обработки детали, т.е. основное время (i).
Цикловая производительность рассчитывается по формуле
Рц(1), (9.2)
где Т — продолжительность рабочего цикла (Т = + = + = /,), мин;
— время холостых ходов рабочей машины, связанных с загрузкой и разгрузкой, межстаночным транспортированием, зажимом и разжимом деталей, т.е. вспомогательное время (‘)
Для большинства автоматическмх линий продолжительность рабочего цикла и всех его элементов остается неизменной в процессе работы машины, поэтому значения технологической и цикловой производительности являются постоянными величинами. В реальных условиях периоды бесперебойной работы рабо-
чей машины автоматической линии чередуются с простоями, вызванными различными организационными причинами. Вследствие этого фактическая производительность линии определяется по формуле
Рф = Кс =
Т + i’обс’
1 (9.3)
где К — коэффициент использования рабочей машины (станка, автомата, ЛИНИИ) во времени.
Коэффициент может быть рассчитан по формуле
к=—-, (9.4)
Т + обс
где 1обс — время внецикловых простоев (обслуживания рабочего места), приходящееся на единицу продукцищ ( определяется по формуле
1обс = тех + (9.5)
здесь 1 — время, затрачИваемое на техническое обслуживание, связанное с регулировкой механизмов, подналадкой и текущим ремонтом оборудования, сменой инструмента и т. д.;
— время, затрачиваемое на организационное обслуживание, обусловленное внешними причинами, которые функционально не связаны и не зависят от конструкции автоматической линии (это отсутствие заготовок, несвоевременный приход и уход рабочего, брак, допущенный на предыдущих операциях, и др.).
С учетом потерь времени только по причинам технического обслуживания определяется потенциальная производительность автоматической линии
(9.6)
Технический уровень автоматической линии (коэффициент технического использования) рассчитывается по формуле
= р / р. (9.7)
Организационно-технический уровень линии (коэффициент общего использования) определяется по формуле
Коргт = Рф / р
(9.8)
Важнейшим календарно-плановым нормативом автоматической линии, характеризующим равномерность выпуска продукции, является такт (или ритм) потока Он определяется суммарньтм временем обработки изделия (‘н), временем установки, закрепления, раскрепления и снятия, а также транспортировки его с одной операции на другую (/):
л = +
(9 9)
Автоматические линии с гибкой связью оснащаются, как правило, независимым межоперационным транспортом, позволяющим передавать детали с операции на операцию независимо друг от друга. После каждой операции на линии создается буикерное устройство (магазин) для накопления межоперационного задела, за счет которого осуществляется непрерывная работа станков.
9.3. Организационно.техническ особенности создания и эксплуатации роторных линий
Разновидностью комплексных автоматических линий являются автоматические роторные линии.
Автоматическ», роторная линия представляет собой комплекс рабочих машин (роторов), транспортных машин (роторов), приборов, объединенных в единую систему автоматического управления, в которой их заготовкм одновременно с обработкой перемещаются по дугам окружностей рабочих роторов совместно с воздействующими на них рабочими инструментами.
Рабочие и транспортные роторы находятся в жесткой кянематической связи и имеют синхронное вращение.
Рабочий ротор представляет собой жесткую систему, на периферии которой на равном расстоянии друг от друга монтируются рабочие инструменты в быстросъемных блоках и рабочие органы, сообщающие инструментам необходимые движения. Каждый инструмент на различных участках своего пути совершает все не-
обходимые элементы движения для выполнения операции Для малых усилий применяются механические исполнительные органы, для больших — гидравлические (например, штоки гидравлических силовых цилиндров).
Инструмент, как правило, монтируется комплексно в блоках, сопрягаемых с исполнительными органами рабочего ротора преимущественно только осевой связью, что обеспечивает быструю смену блоков.
На периферии транспортных роторов на равном расстоянии друг от друга устанавливаются заготовки для изготовления деталей или сборочные единицы для сборки изделий. Транспортные роторы принимают, транспортируют и передают изделия (заготовки) на рабочие роторы. Они представляют собой барабаны или диски, оснащенные несущими органами
Для передачи изделий между рабочими роторами с разными шаговыми расстояниями или различным положением предметов обработки транспортные роторы могут изменять угловую скорость и положение в пространстве транспортируемых предметов.
Рабочие и транспортные роторы соединяются в линии общим синхронным приводом, перемещающим каждый ротор на один шаг за время, соответствующее такту линии (г).
На автоматической роторной линии одновременно можно обрабатывать детали нескольких типоразмеров по сходной технологии, т.е. она может применяться как многопредметная линия и не только в массовом, но и в серийном производстве. В настоящее время такие линии широко применяются для производства радиодеталей, штампованных деталей, при расфасовке, упаковке и на других работах.
Основными календарно-гiлановыми нормативами автоматической роторной линии являются:
1. Такт роторной линии, который определяется временем перемещения заготовки и инструмента на расстояние (4) между двумя смежными позициями ротора (шаг ротора)
грл = ‘пр /
(9.10)
где — транспортная (линейная) скорость движения инструмента (предмета труда), или, что то же самое, окружная скорость ротора, определяемая по формуле
2я
или (9.11)
угловая скорость вращения ротора, оборотов/с или оборотов/мин; радиус ротора, мм или см;
постоянное число, приблизительно равное 3,14;
период вращения (время, за которое ротор совершает полный оборот), с или мин.
Окружные скорости двух роторов (рабочего и транспортного) всегда должны быть равны, это обеспечивает точность позиционирования
(9.12)
где о и п2 — угловые скорости рабочего и транспортного роторов соответственно;
2 — радиусы рабочего и транспортного роторов соответственно.
2. Продолжительность производственного цикла обработки заготовки определяется длиной пути (Ё,) от места загрузки заготовки до места выдачи детали с той же скоростью
(9.13)
Время, в течение которого рабочий инструмент участвует в процессе (р,), больше периода обработки детали (1,) и характеризуется временем полного оборота ротора, т.е.
(9.14)
где — длина полной окружности ротора.
Продолжительность цикла равна сумме входящих в него интервалов, связанных с поворотом ротора на определенный угол
а,.
ци = + + + + + 1 + + 1хд’ (9.15)
где (— передача заготовки из транспортного ротора в инструментальный блок рабочего ротора (а1);
— контроль за правильностью положения, наличием или отсутствием заготовки перед обработкой (а2);
— закрепление заготовки и подвод инструмента (а3);
— время непосредственной обработки детали (а4); 1,,,, — отвод инструмента (а5);
— раскрепление изделия (аб);
— снятие и передача изделия с рабочего ротора в транспортный ротор
(а7);
— холостое движение инструментального блока (а8).
Период холостого хода, соответствующий углу (а8), обычно используется для ручных или автоматических процессов смены инструмента, контроля и очистки от отходов производства.
3. Цикловая производительность роторной машины (два ротора — рабочий и транспортный) определяется по формуле
(9.16)
где п — число рабочих органов (инструментальных позиций) на рабочем роторе.
Цикловая производительность автоматической роторной линии рассчитывается по формуле как величина, обратная такту:
Рцл=1тр/1пр (9.17)
фактическая производительность роторной линии определяется по формуле
Рфл Рцл киев, (9.18)
где К,, — коэффициент использования автоматической роторной линии.
Автоматические роторные линии отличаются определенным уровнем гибкости и позволяют получать достаточно высокие технико экономические показатели. Например, по сравнению с отдельныМи автоматами нероторного типа сокращается производственный цикл в 10—15 раз, уменьшаются межоперационные заделы в 20—25 раз, высвобождаются производственные плошади; снижаются трудоемкость и себестоимость продукции и капитальные затраты окугiаются за 1—3 года.
гдео) —
я—
9.4. Организационно-технические особенности создания и эксплуатации роботизированных
технологических комплексов
В современных условиях равития автомапiзации производства особое место отводится использованию промышленных роботов.
Промь,шлеш,ь,й робот — это механическая система, включаюшая манипуляционные устройства, систему управления, чувствительные элементы и средства передвижения. С помощью промышленных роботов можно объединять технологическое оборудование в отдельные роботизированные технологические комплексы (РТК) различного масштаба, не связанные жестко планировкой и числом комплектующих агрегатов.
Принципиальными отличиями робототехники от традиционных средств автоматизации являются их широкая универсальность (многофункциональносгь) и гибкость (мобильность) при переходе на выполнение принципиально новых операций.
Промышленные роботы находят применение во всех сферах производственно-Хоэяйственн деятельности. Они успешно заменяют тяжелый, утомительцый и однообразный труд человека, особенно при работе в условиях вредной и опасной для здоровья производственной среды. Роботы способны воспроизводить некоторые двигательные и умственные функции человека при выполнении ими основных и вспомогательных производственных операций без непосредственного участия человека. Для этого их наделяют некоторыми способносгями: слухом, зрением, осязанием, памятью и т. д., а также способностью к самоорганизации, самообучению и адаптации к внешней среде.
Промышленный робот — это перепрограммируемая автоматическая машина, применяемая в производственном процессе для выполнения двигательных функций, аналогичных функциям человека, при перемещении предметов труда или технологической оснастки.
Роботы первого поколения (автоматические Манипуляторы), как правило, работают по заранее заданной «жесткой» программе, например в жесткой связи со станками, оснащенными
ЧПУ.
Роботы второго поколения имеют системы адаптивного управления, представленные различными сенсорными устройства-
ми (например, техническим зрением, захватами руками и др.) и программами обработки сенсорной информации.
Роботы третьего поколения обладают искусственным интеллектом, позволяющим выполнять самые сложные функции при замене в производстве человека.
Разнообразие производственных процессов и условий производства предопределяют наличие различных роботизированных технологических комплексов — ячеек, участков, линий и т.д.
Классификация РТК по типу роботизированного подразделения основывается на количественной характеристике выполняемых комплексом технологических операций.
Простейшим типом РТК, положенным в основу более крупных РТК, вплоть до целых предприятий, является роботизированная технологическая ячейка (РТЯ), в которой выполняется небольшое число технологических операций, например роботизированная единица технологического оборудования с ЧПУ.
Более крупный роботизированный комплекс представляет собой роботизированный технологический участок (РТУ). Он выполняет ряд технологических операций (включает несколько единиц РТЯ). Если операции осуществляются в едином технологическом процессе на последовательно расположенном оборудовании, то комплекс представляет собой роботизированную технологическую линию (РТЛ).
Структурно РТК может быть представлен в виде цеха, состоящего из нескольких РТУ, РТЛ, автоматизированных складов и связывающих их транспортных промышленных роботов (роботоэлектрокаров). Высшей формой организации производства является создание комплексно роботизированного завода. В зависимости от вида роботизированного производственного процесса РТК могут быть предназначены для получения заготовок, обработки деталей, выполнения процессов сборки либо для реализации контрольно-сортировочных и транспортноперегрузочных операций, в том числе для внутрицехового транспортирования и складских операций.
При проектировании РТК выделяются два этапа. На первом этапе рассматривают проблемы анализа производства, выбирают объекты роботизации, состав основного технологического оборудования, вид движения деталей, систему рационального автоматизированного управления технологическим процессом и функциональными задачами. На втором этапе осуществляются непос150
редственное проектирование РТК, формируют структуру, определяiот
количество и характеристикм промышленных роботов и
технологического оборудования, разрабатывают рациональные
планировки оборудования РТК в производственном помещении,
составляют и отлаживают алгоритмы и программные системы
управления РТК, необходимые в период функционирования.
Компоновочные вариайты РТК зависят от решаемых технологических
задач, уровня автоматизации, количества и типажа
промышленных роботов, их технических и функциональных возможностей.
Как правило, компоновочные варианты РТК основьтваются
на принципах индивидуального и группового обслуживания
оборудования промышленными роботами.
При индивидуальном обслуживании робот встраивается в
технологическоё оборудование; размещается рядом с оборудованием;
несколько роботов обслуживают единицу оборудования
(рис 9.1,А, Б, В).
При групповом обслуживании робот обслуживает несколько
единиц технологического оборудования; при этом возможны два
варианта коМпоновки: 1) линейное расположение оборудования
(рис. 9.1, Г); 2) круговое расположение оборудования (рис. 9.1, Д).
Выбор оптимальных параметров и рациональных конструкторскмх
решений в период проектирования РТК осуществляется
с учетом нескольких факторов:
производительности ртк, обеспечения надежности его работы,
эффективности функционирования и др. Проектную потенциальнуiо
производительность тя можно определить по формуле
= [ер тех)’ (9.19)
где л’ — число деталей, обрабатываемых за цикл;
Т — цикл работы РТя ((, +
— вречя работы без перерывов за
— время гiростоев, связанных с регулировкой, сменой и подналадкой
инструмента, с отказами устройств РТЯ и т.д.;
ТСХ = об + + 1в Ф Рис. 9.1. Основные варианты компоновочньтх схем РТК
здесь Ё, и /о — потери времени из-за простоев соответственно основ- вейер4-устройствочислового проГраММнО!опраВЛен1я(чпУ),5_МагаЗ1тн
ного технологического оборудования, промышленных инсгрумента(МИ)итательзаготовками(рЭК) 10 накопитель деталей (Н)
роботов и вспомогательного оборудования.
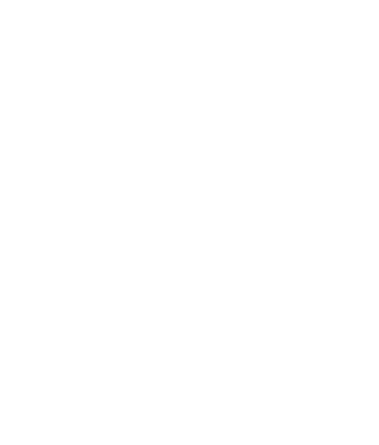
Известно, что кроме перерывов, связанных с техническим обслуживанием (/), технологическое оборудование может простаивать и по причине организационного обслуживания ((). Эти перерывы необходимо учитывать также при определении фактической производительности РТЯ.
Фактическая производительность РТК рассчитывается по
формуле
—---у-к (9.20)
Рпф т отис’
ц
где К0 — коэффициент, учитывающий внецикловые потери рабочего времени (на техническое и организационное обслуживание).
Роботизированная технологическая линия с гибкой межпозиционной связью располагает бункерными устройствами на входе и выходе, а подобная линия с жесткой межпозиционной связью таких накопителей не имеет, и все роботизированные технические ячейки линии должны функционировать синхронно в одном ритме, так как выход из строя любого агрегата или его элемента ведет к остановке данной линии. Исходя из этого при расчете производительности роботизированной технологической линии необходимо определить коэффициент ее технического использования по формуле
(9.21)
+ ртл
где К — коэффициент собственных внециюювых потерь РТЛ, включающих потери времени всеми составляющими элементами РТЛ.
Тогда производительность РТЛ рассчитывается по формуле
Воспользуйтесь поиском по сайту: