Расчет межоперационньих оборотных заделов 3 глава
Н
Рпртл=. Ц (9.22)
црТл
При решении проблем использования РТК особенно важно обеспечить необходимый уровень надежности. Этот комплексный показатель промышленного робота можно определить по формуле
обс
уя= (9.23)
отк воС
где’060 — время, затрачиваемое на техническое и организационное обслуживание РТК в плановый период, ч, смена;
— наработка робота на отказ за плановый период;
— среднее время восстановления работоспособности РТК.
Благодаря повышенной надежности РТК можно снизить потери времени на планово-предупредительные ремонты и ликвидацию аварийных отказов, а таюке уменьшить затраты на ремонт всех видов и техническое обслуживание оборудования. Обеспечение ритмичности производственного процесса в условиях РТК и синхронизация операций представляют собой сложные организационные задачи, для РТК устанавливают размер усредненного такта или ритма (,) и за счет группирования и подбора операций обеспечивают равенство или кратность между продолжительностью операций и тактом, который определяется по форму-
ле
ус = Iыт 1 / р тя’ (9.24)
где — штучное время на выполнение i-й операции С — число роботизированных технологических ячеек.
За счет синхронизации простои основного оборудования РТК сводятся к минимуму, при этом увеличиваются его производительность и эффективность.
9.5. Организационно-технические особенности создания и эксплуатации гибких
производственных систем
В современных условиях сфера распространения поточных форм организации производства и соответствующих видов поточных линий (ОНПЛ, ОППЛ, МНПЛ, МППЛ, автоматических линий и автоматических роторных линий) ограничена в основном массовым и крупносерийным производством, доля которого в общем объеме производства не столь значительна и постоянно уменьшается под воздействием факторов, обусловленных научно-техническим прогрессом. К таким факторам относятся: рост много-
‘ч
образия разработки объектов новой продукции; частая сменяемость выпускаемых изделий; увеличение номенклатуры производства изделий, сборочных единиц и деталей; снижение объема выпуска отдельных изделий при увеличении объема других и т. д. Развитие радиозлектроники, вычислительной техники и программирования, серийное производство высокопроизводительных многоцелевых станков с ЧПУ (обрабатывающих центров), робототехника и использование групповой технологии — все это потребовало создания базы для автоматизации серийного, мелкосерийного и единичного производств, а также для перехода к гибкому автоматизированному производству и массовому внедрению гибких производственных систем (ГПС).
В отличие от поточных и автоматических линий, специализирующихся только на изготовлении определенного вида изделий, ГПС обеспечивают выпуск серийных и мелкосерийных изделий дискретными партиями, номенклатура и размеры которых могут меняться во времени. При этом использование ГПС в многономеиклатурном производстве должно способствовать сохранению отличительных особенностей и преимуществ массового производства (непрерывности и ритмичности) и существенному повышению производительности труда и качества выпускаемой продукции при сокращении численности рабочих-операторов.
Гибкие производственные системы отличаются от технических систем, состоящих из универсального оборудования и автономно работающих станков с ЧПУ, и от производств, оборудованных станками-автоматами и полуавтоматами в линии (автоматические и автоматические роторные линии и др.) с механической связью. От производств, оснащенных универсальным оборудованием и станками с ЧПУ, ГПС отличаются высокой производительностью оборудования и труда за счет того, что одновременно могут выполнять много операций производственного процесса с одной установки обрабатываемого предмета труда, а также работать в автоматическом режиме круглосуточно. От автоматических линий ГИС отличается гибкостью в широком смысле слова, что позволяет обрабатывать в ней изделия широкой номенклатуры и быстро менять объекты производства.
Обладая широкой гибкостью, ГПС обеспечивает высокую производительность оборудования, приближающуюся к уровню производительности автоматических линий и линий, скомпонованных из специализированных станков. Основной показатель
ГПС — степень гибкости — может быть определен затрачиваемым временем или количеством необходимых дополнительных асходов при переходе на выпуск изделий определенного наименования, а также широтой номенклатуры выпускаемой продукции.
Степень гибкости производственной системы — это не однозначный, а многокритериальный показатель. В зависимости от конкретно решаемой задачи ГПС выдвигаются различные аспекты гибкости:
1) машинная гибкость — простота перестройки технологического оборудования для производства заданного большого количества изделий каждого наименования;
2) технологическая гибкость — способность системы производить заданное большое количество деталей каждого наименования при различных вариантах технологического процесса;
З) структурная гибкость — возможность расширения ГПС за счет введения новых дополнительных технологических модулей, а также объединения нескольких систем в единый комплекс;
4) гибкость по объему выпуска — способность системы экономично изготавливать изделия каждого наименования при разных объемах партий запуска и может быть охарактеризована минимальным размером партии, при котором использование системы остается кономическi4 эффективным;
5) гибкость по номенклатуре — способность системы к обновлению выпуска продукции, характеризуется сроками и стоимостью подготовки производства деталей нового наименования. В мелкосерийном производстве в качестве показателя гибкости номенклатуры можно принять максимальный коэффициент обновления продукции, при котором использование системы остается экономически эффективным.
Важное значение для обеспечения гибкости по номенклатуре имеет унификация конструктивных и технологических решений, достигаемая за счет автоматизации процессов конструирования изделий и технологической подготовки производства, а также широкого применения принципов групповой технологии, являющейся технологическим фундаментом современных механообрабатывающих производств.
Перечисленные виды гибкости тесно связаны между собой и улучшение одного показателя гибкости может вызвать ухудшение другого. Поэтому при сопоставлении различных ГПС, особенно при анализе вариантов на стадии проектирования, жела-
тельно пользоваться не качественными оценками, а некоторой системой количественiIых характеристик, так как создание ГПС, обладающих высокой гибкостью по всем перечисленным показателям, является не только технически невозможным, но и экономически нецелесообразным. Поскольку каждая ГПС разрабатывается для нужд конкретного предприятия, цеха, участка, она оказывается специализированной не только по своему технологическому назначению, но и решаемым производственным задачам.
В общем виде под ГПС понимается автоматизированное производство, построенное на современных технических средствах (станках с ЧПУ, роботизированных технологических комплексах, гибких производственных модулях, транспортно-накопительньтх и сютадских системах и др.), способное обеспечивать выпуск продукции широкой номенклатуры, однородной лишь по своим основным конструктивным и технологическим параметрам и способное безынерционно переходить на выпуск новых изделий любого наименования, К основным факторам, обеспечивающим функционирование ГПС, относятся: 1) комплексная автоматизация всех основных и вспомогательных технологических операций; 2) программная переналадка технологического оборудования; 3) оперативная (автоматизированная) конструкторско-технологическая и организационно-экономическая подготовка производства; 4) автоматизация управления производственно-техно логическими процессами, осуществляемая в режиме реального времени; 5) реализация и оптимизация оперативно-производ ственного планирования, позволяющая максимально загрузить оборудование, минимизировать производственный цикл и обеспечить комплектность деталей и сборочных единиц для сборки; б) групповая технология обработки деталей.
Реализация перечисленных выше факторов осуществляется за счет функциональных элементов ГПС, которые можно разделить на две группы:
• производственнотехнологиеские функциональные элементы гибкого автоматизированного производства (ГАП), составляющие производственно-технологическую часть ГИС;
• электронно-вычислительные функциональные элементы ГАП, составляющие информационно-вычислительную и управляющую часть ГИС.
При проектировании производственно-технологической части ГПС, как правило, используют блочно-модульный принцип на различных организационных уровнях системы (рис. 9.2).
Рис. 9.2. Структура гибкой производственной системы:
ГГ]К — гибкий производственный комплекс, ГАд — гибкая автоматизированная линия, [АУ — гибкий автоматизированный участок, ГАЦ — гибкий автоматизированный цех
Основными элементами производственно-технологической части ГИС являются: гибкий производственный модуль (ГПМ), роботизированный технологический комплекс (РТК) и система обеспечения функционирования.
Гибкий производственный модуль — это единица технологического оборудования с ЧПУ для производства изделий произвольной номенклатуры в установленных пределах значений их характеристик, автономно функционирующая, автоматически осуществляющая все функции, связанные с изготовлением продукции и имеющая возможность встраиваться в более сложную
ГПС.
В состав ГПМ входят специальное технологическое оборудование (от одного до трех станков с ЧПУ); контрольно-измерительная аппаратура и установки; промышленные роботы и манипуляторы; средства автоматизации технологического процесса; средства идентификации деталей, заготовок, инструмента и оснастки.
Роботизированный технологический комплекс — это совокуо— ность единиц технологического оборудования от З до 10 станков с ЧПУ, роботов и средств их оснащения. Этот комплекс автоном158
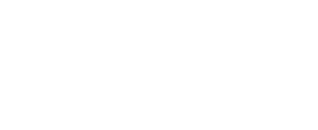
но функционирует и осуществляет многократные циклы. Предназначенные для работы в ГПС роботизированные комплексы должны иметь автоматизированную переналадку и возможность встраиваться в ГПС. В качестве средств оснащения эти комплексы могут быть устройствами накопления, ориентации, поштучной выдачи объектов производства и др.
Таким образом, основными характеристиками ГПМ и РТК являются:
• способность работать автономно, без участия человека;
• автоматически выполнять все основные и вспомогательные операции производственного процесса;
• гибкость, удовлетворяющая требованиям единичного и мелкосерийного производств;
• простота наладки и возможность устранения отказов основного оборудования и системы управления;
• совместимость с оборудованием традиционного и гибкого производства;
• высокая степень завершенности обработки деталей с одного установа;
• высокая экономическая эффективность при правильной эксплуатации.
В настоящее время создаются и эксплуатируются ГПС полного технологического цикла, на которых детали или изделия обрабатываются (изготавливаются) со 100%-ной готовностью, и ГПС неполного цикла, когда для завершения изготовления детали требуются дополнительные операции, выполняемые вне данной системы. В соответствии с этим создаются более сложные ГПС в виде гибких производственных комплексов (ГИК), гибких автоматизированных линий (ГАЛ), гибких автоматизированных участков (ГАУ), гибких автоматизированных цехов (ГАЦ) и гибких автоматизированных заводов (ГАЗ).
ГПК — это гибкая производственная система, состоящая из нескольких ГИМ (треть парка от — б до 10 ГИМ, а остальные — 11 ГПМ и более) или РТК, объединенных АСУ и автоматизированной транспортно-складской системой (АТСС), автономно функционирующая в течение заданного времени и имеющая возможность встраиваться в систему более высокого уровня автоматизации.
ГАЛ — ГИС, включающая несколько ГИМ или РТК, объединенных АСУ, в которой технологическое оборудование располагается в принятой последовательности технологических опера-
ций вдоль автоматизированной транспортно-накопительной системы.
ГАУ — ГПС, состоящая из нескольких ГИМ, РТК, ГАЛ и отдельных единиц специального технологического оборудования, автоматизированной транспортно-накопительной системы, объединенных АСУ в гибкий участок, в котором предусмотрено изменение последовательности использования технологического оборудования в пределах заданного технологического маршрута.
ГАЦ — ГПС, объединяющая ГАУ (или ГАЛ), вспомогательные участки и отдельные ГИМ, ГПК и АТСС. Управляется автоматизированной системой.
ГАЗ — ГПС, состоящая из ГАЦ заготовительного производства, ГАЦ обрабатывающей и сборочной стадий, автоматизированных складов материалов, заготовок, комплектующих изделий, готовых деталей и изделий, автоматизированной транспортной системы (АТС). Объединяется АСУ.
Система обеспечения функционирования ГПС в автоматическом или автоматизированном режиме включает: а) автоматизированную трансгюортно-складскуЮ систему, т. е. систему взаимосвязанных автоматизированных транспортных и складских устройств с установкой в транспортной таре для временного накопления, распределения и доставки предметов производства и технологической оснастки к ГПМ, РТК или другому технологическому оборудованию в ГПС; б) автоматизированную систему инструментального обеспечения (АСИО), осуществляющую подготовку, хранение и автоматическую замену инструмента; в) автоматизированную систему слежения за износом и поломками инструмента (АССИ); г) автоматизированную систему обеспечения надежности, следящую за состоянием оборудования (АСОН); д) автоматизированную систему управления качеством продукции (АСУКП); е) автоматизированную систему удаления отходов производства (АСУОП).
Производственнотехнологическая часть ГИС предназначена для выполнения всех основных и вспомогательных технологических процессов и операций над элементами материального потока.
Основным элементом информационновычислительной и управляющей части ГИС является автоматизированная система управления предприятием (АСУП), обеспечивающая автомати-
зированное организационно-экономическое управление гибким автоматизированным производством и включающая системы более низкого уровня, такие как:
• система автоматизированного проектирования (САПР);
• автоматизированная система технологической подготовки производства (АСТПП);
• автоматизированная система управления технологическими процессами (АСУТП);
• автоматизированная система научных исследований (АСНИ);
• локальные системы управления (ЛСУ).
Частичная или полная интеграция производственно-технологической части ГПС с функциональными системами информационно-вычислительной и управляющей частей в единую производственную систему превращает ее в гибкое автоматизированное производство.
И нформационно-вычислительная и управляющая части ГПС обеспечивают управление и координацию деятельности производственно-технологических функциональных элементов системы, которая реализуется иерархией ЭВМ.
На первом уровне иерархии управления используются ЧПУ. С их помощью управляются станки и другое технологическое оборудование, промышленные роботьт, роботоэлектрокары и прочие транспортные системы.
На втором уровне используются микро-ЭВМ типа «Электроника» и другие программно совместимые с ней ЭВМ. С их помощью управляются ГПМ, РТК, АТС, АСС и прочие обеспечивающие системы.
На третьем уровне используются мини-ЭВМ типа СМ-1420 и другие программно совместимые с ними ЭВМ. Мини-ЭВМ управляют группами модулей (ГПК, ГАЛ, ГАУ, ГАЦ). На этом уровне с помощью мини-ЭВМ осуществляются хранение программ и другой информации, реализация оперативно-календарного плана, регистрация текущего состояния производства, контроль за неисправностью оборудования и т.д.
На четвертом уровне используются мощные ЭВМ в составе
АСУП.
На всех этапах разработки ГПС рассматриваются как сложные производственные системы, в состав которых входят производственно-технологические и электронно-вычислительные элементы ГАП, предметы труда и обслуживающий персонал, а также система управления.
9.6. Оценка экономического эффекта от использования средств
томотизации производства
При проведении работ на конкретном предприятии с целью перехода на 0маТизированное производство возникает вопрос об оценке капитальных затрат на внедрение средств томатизациИ и определении эффективности этих затрат. для этого необходимо установить структурУ затрат на создание 0атИзированного производства (автоматичесх и Воматичесх роторных ЛИНИЙ, РТК, ГПС) и процедуру определения эффективности этих затрат.
Соизмерение затрат и результатов при создании автоматизированного производства является частью общей проблемы, рассматриваемой в теории экономической эффективности капитальных вложений.
Техничск14й уровень современного производства позволяет оматизировать почти любую технологическую операцию. однако далеко не всегда оматизация при этом будет экономичес ки эффективной томатизация производства может осуществляться с применением различного оборудования, разных средств оматизации, транспортных и контрольных устройств, любой компоновки технологического оборудования и т.д. Поэтому необходимо правильно выбрать варианты матизации производства и дать комплексную оценку их экономической эффективности.
Экономическая эффективность маТИзации производства оценивается показателями в стоимостном и натуральном выражении, к основным стоимостным показателям относятся себестоимость продукции, капитальные затраты, приведенные затраты и срок окупаемости дополнительных капитальных вложений в средства автоматизации.
При обосновании экономической целесообразности создания и эксплуатации автоматической или 0Матизированной производственной системы необходимо исходить из следующих основных принципов теории экономической эффективности капитальных вложений.
1. Экономический эффект от использования средств автоматизации — это экономия общественного труда при производстве каких-либо видов продукции. Экономия труда или экономия времени коренным образом определяет направленность капитальных вложений.
163
2. Целесообразность использования средств автоматизации на конкретном предприятии (в цехе) обосновывается соотношением хозяйственного эффекта и затратами по каждому варианту.
3. В качестве критерия сравнения вариантов принимаются приведенные затраты, отражающие текущие затраты и капитальные вложения.
При экономическом обосновании целесообразности использования средств автоматизации в конкретном производстве следует учитывать:
• экономический эффект в сфере производства продукции, в условиях автоматизации;
• сравниваемые варианты, предлагаемые для организации производства продукции, приведенные к тождественному эффекту;
• цель внедрения средств автоматизации — увеличение объема и качества выпускаемой продукции на базе интенсификации;
• выбор наилучшего варианта из двух рассматриваемых, которому соответствует минимум приведенных затрат.
Формула приведенных затрат позволяет соимерять разнородные по своему характеру величины — текущие (себестоимость продукции) и единовременные затраты (капитальные вложения в средства автоматизации) — путем отнесения их на годовой объем производства продукции либо (при использовании вместо нормативного коэффициента эффективности нормативного срока окупаемости) на весь срок работы средств автоматизации производства, в течение которого стоимость должна окупиться за счет снижения текущих затрат (себестоимости продукции) При этом величина годового экономического эффекта (Э, руб./год) от применения средств автоматизации производства определяется по формуле
Э = (С1 + ЕК1) — (С2 + ЕК2),
(9.25)
где С1 и С2 — себестоимость годового выпуска продукции соответственно до и после внедрения средств автоматизации производства, руб./год,
К1 и К2 — капиталовложения соответственно до и после внедрения средств автоматизации, руб.;
Е — нормативный коэффициент сравнительной экономической эффективности капитальных вложений.
Положительное значение разности приведенных затрат свидетельствует об экономической целесообразности внедрения системы автоматизированного производства. Кроме того, определяют вспомогательные показатели с учетом особенностей производства: такт (ритм) потока, часовую производительность производственную мощность, численность обслуживающего персонала, трудоемкость обработки, выработку на одного работаюшего, продолжительность производственного цикла, величину незавершенного производства, занимаемую производственную площадь, съем продукции с 1 м2 производственной площади, коэффициент сменности и др.
При расчете величины годового экономического эффекта должно быть соблюдено условие сопоставимости неавтоматизированного и автоматизированного производств. Схема приведения вариантов в сопоставимый вид представлена на рис. 9.3.
Сопоставимость означает, что сравниваемые варианты рассчитаны на годовой выпуск равного количества продукции с одинаковыми техническими характеристиками. При этом из всех расчетов должно быть исключено влияние стоимостных факторов, т.е. цены на сырье и материалы, электроэнергию и другие элементы себестоимости во всех вариантах должны приниматься одинаковыми. Только при таком условии можно проводить технико экономическое сопоставление вариантов.
Текущие затраты по базовому (существующеiу) варианту с учетом приведения к тождественному эффекту по объему продукции и качеству (С1) определяются по формуле
С1 = С’1(1Ч, о) + АС’1 + АС’2,
(9.26)
где С’1(Н1, о) — текущие затраты на годовой объем выпуска продукции до внедрения средств автоматизации производства, руб /год,
— дополнительные текущие затраты, которые были бы необходимы для выпуска дополнительного объема продукции ЛI\, на который увеличится объем выпускаемой продукции в условиях автоматизированного производства, руб./год
— дополнительные текущие затраты, которые были бы необходимы для повышения качества выпускаемой продукции до уровня (е), достигаемого в условиях автоматизированного производства.
Сколько необходимо иметь
дополнительных текущих
затрат и капитальных
вложений, чтобы объем
производства
и технический уровень
выпускаемой продукции
при существующей
производственной системе
достигли уровня при автоматизированной
системе
Приведенные Приведенные
затраты _______ затраты
для базового Сравнение *— для проектируемого
варианта _________________ 1 варианта
Выводы
Рис. 9.3. Схема приведения вариантов к тождественному эффекту
Капитальные вложения по базовому (существующему) варианту с учетом приведения к тождественному эффекту (К1) определяются по формуле
К1 = К’1(IЧ, д1) + ДК’i +
(9.27)
где К’1(Н1, ф1) — капиталовложения в производственную систему по базоному варианту до внедрения средств автоматизации, руб.;
АК’1 — дополнительные капиталовложения, которые были бы необходимы для выпуска дополнительного объема продукции, на который увеличится объем продукции в условиях 0ати3ированного производства, руб.;
АК’2 — дополнительные капиталовложения, которые были бы необходимы, чтобы повысить качество выпускаемой продукции до уровня, достигаемого в условиях автоматизированного производства, руб.
Текущие затраты по второму (проектируемомУ) варианту (С2) рассчитываются по формуле
с2 = С(Рi2, ф2) + С31,
(9.28)
где С’2(1Ч2, ф2) — текущие затраты на годовой объем выпуска продукции повышенного качества после внедрения средств автоматизации производства, руб./год
— текущие затраты на содержание и эксплуатацию средств автоматизации производства, руб./год.
Капитальные вложения по второму (проектируемому) варианту (К2) определяются по формуле
К2 = К’(Рi2, ф2) + Кант — ДО0,
(9.29)
где К’2(1У2, 0>2) — капиталовложения в производственную систему по проектируемому варианту после внедрения средств автоматизации, руб.;
Кант — капитальные затраты, необходимые для реализации мероприятий по внедрению средств томатизации, руб.;
— оборотные средства, высвобождаемые в результате автоматизации производства, руб.
Преобразовав формулу (9.25), получим новую формулу для расчета величины годового экономического эффекта
Э = [С’1(1Ч1, ф1) + ДС’1 + ДС’2 — С’2 — С’2(IЧ2, (1)2) — —
— Е[К’2(Н2, (2) + Ка — АО0 — К1(ЛТ1, (i) ДК’1 АК’2]. (9.30)
Размер дополнительных текущих затрат (ДС’) определяется по формуле
167
Базовый вариант:
существующая
производственная система
Текущие Капитальные
затраты вложения
‘4,
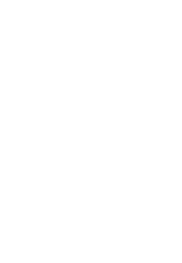
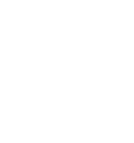
лс =$л1ч,,
(9.3 1)
где — удельная себестоимость продуклии-го наименования, руб.; ЛЛ — дополнительный объем продукции]-го наименования, который может быть выпущен в условиях автоматизации производства, шт./год;
т — число наименований продукции, выпускаемых производственной системой.
Размер дополнительных текущих затрат (‘‘С2) рассчитывается по формуле
с’2
(9.32)
где — затраты на повышение качества единицы научно-технического уровня продукции]-го наименования, которые были бы необходимы в базовом варианте для доведения уровня качества до его значения в условиях автоматизированного производства;
Ло1 — приращение научно-технического уровня продукции 1-го наименования по сравнению с тем, которое будет иметь место в условиях автоматизированного производства, ед.
Текущие затраты на содержание и эксплуатацию средств автоматизации определяются по формуле
сэкс=3i +32+33+34+35+36,
(9.33)
где 3 — затраты на техническое обслуживание средств автоматизации (прямая и дополнительная заработная плата персонала, обслуживающего средства автоматизации с начислением налогов), руб./год;
— амортизационные отчисления от стоимости средств автоматизации, руб./год;
3 — затраты на электроэнергию, потребляемую техническими средствами, руб/год;
34 — затраты на выполнение профилактических и текущих ремонтов, руб /год
35 — затраты на вспомогательные материалы и другие технические средства, необходимые для нормального функционирования средств автоматизации, руб./год;
Эб — прочие затраты на эксплуатацию средств автоматизации (затраты на содержание помещения, освещение, вентиляцию и др.), руб/год.
Затраты на техническое обслуживание средств автоматизации
3 + Ч2’С,,Кпрем)(I4Ндз н)’
1=1 1=1
(9.34)
где Ч1, — численность инженерно-технических работников (ИТР) 1-Й категории, обслуживающих технические средства автоматизации;
— годовой фонд заработной платы инженернотехнических работников ‚-Й категории, руб./чел.;
Ч2, — численность рабочих ‚-го разряда, обслуживающих технические средства;
С, — часовая тарифная ставка рабочего i-го разряда, руб./чел.-ч,
Рэфi — годовой эффективный фонд времени рабочего 1-ГО разряда, ч/год;
— коэффициент, учитывающий премии по премиальным системам
з — коэффициент, учитывающий размер дополнительной заработной платы и отчислений в фонд социальной защиты и другие налоги;
п — число категорий инженерно-технических работников и разрядов рабочих.
Амортизационные отчисления
=
.1=1
(9.35)
где К — балансовая стоимость технического средства автоматизации л-го вида;
— количество технических средств ]-го вида, используемых в автоматизированной производственной системе;
На] — норма амортизационньтх отчислений для технических средств автоматизации /-го вида, %;
с — число видов технических средств в производственной системе
О = 1,2,.., с).
Затраты на электроэнергию
= игР3фц3$К3
(9.36)
где ИГ — установленная мощность комплекса технических средств автоматизации, кВт;
Р3ф — годовой эффективный фонд времени работы технических средств в одну смену, ч;
З — число рабочих смен в сутках;
Ц, — тариф за 1 кВт ч электроэнергии, руб.;
— коэффициент учитывающий использование энергии по времени;
к3 — коэффициент, учитывающий использование энергии по мощности;
— коэффициент загрузки технических средств автоматизации; 1 — коэффициент, учитывающий потери электроэнергии в сети; т — КПД технических средств автоматизации производства.
Затраты на текущий ремонт и профилактику
й
34 = 1УрiЦр,,
1=1
(9.37)
где 2У, — число ремонтов технических средств 1-го вида в год;
Ц1,, — средняя стоимость одного ремонта технических средств 1-го вида,
руб.;
й — число видов ремонтов.
Затраты на вспомогательные материалы и оборудование
Воспользуйтесь поиском по сайту: