Понятие и система показателей качества продукции
Понятие «каче9тво продукции» — экономическая категория и как объект экономической науки тесно связана с категорией потребительной стоимости и проявлением последней лишь в процессе использования этой стоимости (продукции). К. Маркс писал:
«Полезность вещи делает ее потребительной стоимостью. Но эта полезность не висит в воздухе. Обусловленная свойствами товарного тела, она не существует вне этого последнего. Поэтому товарное тело... само есть потребительная стоимость или благо».
Потребительная стоимость характеризуется двояко: с одной стороны, как вещь или материальный предмет; а с другой — как
вещь, которая способна соответственно своими свойствами удовлетворить определенные человеческие потребности, т.е. как полезная вещь.
Таким образом, экономическое содержание категории качества обусловливается оценкой 0бщественной пол езности продукта. Мерой общественной полезности продукта является общественно необходимое качество. Оно предопределяет достижение такого уровня потребительских свойств продукции, который обеспечил бы удовлетворение потребностей общества при наиболее рациональном использовании имеiбщихся в его распоряжении материальных, финансовых и трудовых ресурсов.
К. Маркс писал: «Продукт, потребительские свойства которого выше потребительских свойств других продуктов одинакового назначения, признается продуктом более высокого качества. Здесь существенны не сами свойства продукта, а, именно, потребительские свойства продукта, в какой мере и в какой степени они способны удовлетворять конкретную потребность общества. Потребителя не интересует природа предмета потребления как таковая, для него ВаЖНО, чтобы данная потребительная стоимость обладала нужными ему свойствами. Совокупность определенных полезных свойств продукции и делает ее предметом потребления. Оценка потребительной стоимости по степени удовлетворения конкретной потребности определяет ее качество.
Качество продукций площает степень, меру, в которой она объективно удовлетворяет данную потребность. Здесь речь идет о качестве продукгIии как о количественной характеристике общественной потребительной стоимости, степени полезности продукта труда. Вместе с тем не только потребительские свойства самого продукта определяют его качество. Свойства МОГГ оставаться теми же самыми, в то время как степень удовлетворения потребности в данном продукте в результате появления новых общественных потребностей будет меняться. Например, производство телевизоров черно-белого, а затем цветного изображения.
до времени среди специалистов нет единства в определении понятия «качество продуии». Как правило, эти определения Неполны, ногообразнь1, неточны, но в каждом случае они отвечают конкретным потребностям общества. для определенных условий совместной деятельности людей терминологию понятий необходимо конкретизировать или стандартизи ровать.
231
На наш взгляд, наиболее точное определение понятия «качество продукции» дано в ГОСТ 15467-79 «Управление качеством продукции. Термины и определения». В нем кроме определения приведены разъяснения свойств, показателей и уровня качества продукции. Согласно этому стандарту качество продукции — это совокупность свойств продукции, обусловливающих ее пригодность удовлетворять определенные потребности в соответствии с ее назначением.
Под свойством продукции понимается объективная особенность последней, проявляющаяся при ее производстве, эксйлуатации или потреблении. В этой связи необходимо различать производственные и потребительские свойства продукции.
К производственным относится вся без исключения совокупность свойств продукции, создаваемых в процессе производства. Это потенциальное качество.
Потребительские свойства и характеристики продукции определяют лишь ту совокупность показателей, которая относится к числу наиболее важных и значимых для потребителя. Это реальное качество продукции.
Следовательно, можно сказать, что продукт труда, созданный в процессе производства, до его реализации обладает только потенциальным качеством, которое переходит в реальное качество, лишь вступив в процесс реализации и потребления, т.е. когда данный продукт начинает участвовать в удовлетворении конкретных общественных потребностей. Если эта потребность не удовлетворяется, ни о каком качестве говорить не приходится.
Количественная характеристика свойств продукции (технических, экономических и др.) называется показателем качества продукции.
По количеству характеризуемых свойств и характеристик все показатели качества делятся на единичные, комплексные, определяющие и интегральные.
Единичные показатели качества отражают одно свойство продукции (например, скорость, потребляемая мощность и др.).
Комплексные показатели качества характеризуют совокугiность нескольких свойств продукции (например, надежность, воспроизведение телевизором типовой испытательной таблицы и др.).
Определяющие показатели качества — оценочные показатели, по которым принимаются решения о качестве.
Интегральные показатели качества выражаются через соответствуIощую сумму экономических или технических показателей (например, суммарный полезный эффект от эксплуатации продукции, суммарные затраты на создание и эксплуатацию изделия).
Для продуии машиностроения может быть установлена следующая номенклатура показателей качества рис. 15.1).
Числовые значения показателей качества измеряются с помощью приборов, измерительных инструментов, опытным или расчетным путем и представляются в единицах физических величин в натуральном или стоимостном выражении.
Показатели качества изделия
Производственная группа Потребительская группа
Технологичности Надежности
Технического уровня
Капиталовложения ф Капиталовложения, связанные
в производство изделия с эксплуатацией изделия
Себестоимость и оптовая Себестоимость единицы
цена изделия (продукции), выполняемой
изделием
Производительность труда
Рентабельность
Рис. 15.1. Система показателей качества продукции

Для оценки некоторых свойств продукции, например эстетических, технические средства неприемлемы, и их измерение проводится органолептическим методами (с помощью органов чувств по балльной системе). Иногда свойства продукции оцениваются путем социологических опросов потребителей или методом экспертных оценок.
Приведенная на рис. 15.1 система показателей качества про— дукции является основной для количественной оценки и определения уровня качества конкретного вида продукции. При этом уровень качества изделия может оцениваться в зависимости от поставленной цели дифференцированно либо по единичным, комплексным или интегральным показателям качества, либо по производственной или потребительской группе.
Уровень качества — это относительная характеристика качества, основанная на сравнении значений показателей качества оцениваемой продукции с соответствующими показателями продукции, принятой за базу для сравнения.
Наряду с уровнем качества определяется технический уровень продукции. Оценка последнего обычно проводится при разработке новых или атгестации серийно выпускаемых изделий по номенклатуре технических показателей, представленньтх на рис. 15.1.
15.2. Эволюция подходов к управлению
качеством продукции
Эволюцию подходов к управлению качеством продукции на отечественных предприятиях можно проследить, начиная со времени Ивана Грозного, когда по его указанию впервые были введены стандартные калибрьи-кружала для измерения диаметров пушечных ядер, а при постройке сторожевого городка Свияжска — строительные элементы, заранее изготовленные по стандартным размерам в г. Угличе. Однако этот период характерен только для отдельных стандартизированных решений. Начало более широкому внедрению стандартизации в производство с целью повышения качества продукции было положено Петром 1, во времена правления которого начинается отсчет русской промышленной стандартизации.
В первом собрании законов Российской империи эпохи Петра 1 имеется ряд указов, свидетельствующих о том, что в это время в России внедрялись элементы стандартизации и взаимозамещаемости с целью повышения качества продукции, выпускаемой на отечественных предприятиях. В контексте рассматриваемого вопроса об отечественном опыте государственного управления качеством прсДукции несомненный интерес представляет Указ Петра 1 о качестве от 11 января 1723 г. Из текста Указа ясны не только требования Государя к качеству продукции, но и к системе контроля качествi, государственного надзора за ним и меры ответственности и наказания за выпуск недоброкачественной продукции.
Стремясь к расширению внешней торговли, Петр 1 не только ввел технические условия, учитывающие высокие требования иностранных рынков к качеству товаров, но и организовал в Петербурге и Архангельске правительственные бракеражные комиссии, которым вменялось в обязанность следить за качеством экспортируемого Россией сырья (льна, древесины) и других видов продукнии.
Развитие промышленности и транспорта в России привело к расширению работ по стандартизации. В 1860 г. был установлен единый размер железнодорожной колеи (1524 мм) и утверждены габаритные нормы приближения строений и подвижного состава. В 1889 г. приняты первые технические условия на проектирование и сооружение железнодорожных путей, а в 1898 г. — единые технические требования к поставке основных материалов и изделий для нужд железнодорожного транспорта. В 1899 г. был выпущен единый сортамент профилей прокатной стали.
Внедрение российских национальных стандартов и единых требований к качеству продукции в дореволюционной России затруднялось из-за большого числа иностранных концессий, владельцы которых применяли, как правило, свои стандарты. Такое положение привело, в частности, к распространению в России трех систем мер (аршинной, дЮЙМОВОЙ, метрической), затруднявших производство продукции и контроля ее качества.
Одним из первых после Октябрьской революции был принят декрет «О введении международной метрической системы мер и весов» (14 сентября 1918 г.), имевший важное значение для развития стандартизации и повышения качества.
В 1926 г. был утвержден первый общесоюзный стандарт ОСТI «Пшеница. Селекционньте сорта зерна. Номенклатура», В том же году были приняты стандарты на новый сортамент стального проката, что позволило сократить число типоразмеров профилей в б раз, а также стандарты на метрическую и дюймовую резьбу, на допуски и посадки, благодаря чему было налажено серийное и массовое производство стандартных общемашиностроительных деталей. Эти стандарты послужили основой для овладения методами передовых зарубежных фирм по контролю качества продукции на основе системы допусков и посадок. Таким образом, одной из первых форм управления качеством продукции стала проверка изделий методом сортировки и разбраковки на годные и негодные, т.е. соответствующие и несоответствующие стандарту
К началу 1975 г. в СССР действовало уже более 20 тыс, стандартов, охватывающих важнейшие виды промышленной и сельскохозяйственной продукции, более 15 тыс. отраслевых стандартов и свыше 100 тыс. технических условий.
для планомерного повышения качества выпускаемой продукции были введены атгестация промышленной продукции по высшей, первой и второй категориям качества и присвоение Государственного знака качества.
Однако множество разработанных стандартов и атгестация промышленной продукции на категории качества не привели к желаемому результату так как проводились без системного подхода и лишь на одной стадии «жизненного цикла» изделия — на стадии производства. Практика показывает, что только систем- ный подход к управлению качеством позволяет добиваться положительных результатов.
Проследим эволюцию воплощения системного подхода к организации работ по улучшению качества продукции в отечественной практике последних лет.
В 1955 г. на предприятиях г. Саратова были разработаны и внедрены организационнотехничес мероприятия по обеспечению бездефектного изготовления продукции и сдачи ее в отдел технического контроля (ОТК) с первого предъявления, В своей совокупности они образовали саратовскую систему управления качеством продукции (систему БИП).
В 1957—1958 гг. на предприятиях г. Горького (теперь Нижний Новгород) появилась система КАНАРСПИ (качество, надежность, ресурс с первого изделия). В этой системе был сделан упор
на повышение надежности изделий в эксплуатации за счет укрепления технической подготовiо{ производства, на долю которой приходилось 60—85% дефектов, обнаруживаемых при эксплуатации. Создавались опытные образцы узлов, деталей, систем и изделия в целом и проводились их испытания, выявлялись причины, вызывающие отказы изделия при эксплуатации, разрабатывались мероприятия по их устранению.
Внедрение системы КАНАРСПИ на ряде предприятий Горьковской области позволило сократить сроки доводки новых изделий до заданного уровня качества в 2—3 раза; повысить надежность выпускаемых изделий в 1,5—2 раза; увеличить ресурс в 2 раза; снизить трудоемкость и цикл монтаж”осборочных работ в 1,3—2 раза.
В 1963—1964 гг. на ярославском моторном заводе была разработана и внедрена система НОРМ (научная организация труда по увеличению моторесурса). Цель системы — увеличение надежности и долговечности выпускаемых двигателей. В ней был учтен опыт предшествовавших систем БИП и КАI—IАРСПИ и введен новый важный элемент — управление связями между потребителями изделий и проектировщиками. В основу системы НОРМ был положен принцип последовательного и систематического контроля за уровнем моторесурса и периодическим его увеличением на базе повышения надежности и долговечности деталей и узлов, лимитирующих моторесурс. Основным показателем являлся ресурс двигателя до первого капитального ремонта, выраженный в моточасах. Рост этого показателя в системе планировался.
В 1975 г. на предприятиях Львовской области появились комплексные системы управления качеством продукции (КСУКП). Целью этой системы было создание продукции, соответствующей лучшим мировым аналогам и достижениям науки и техники.
В настоящее время созданы и функционируют комплексные системы управления качеством на уровне предприятия, а также на всех стадиях создания и использования продукции — при исследовании и проектировании, изготовлении, обращении и реализации, эксплуатации или потреблении.
На уровне предприятия управляющую систему представляют, технические отделы (отдел главного конструктора и отдел главного технолога), службы надежности, стандартизации, метроло236
гии, служба (отдел) технического контроля качества и др. К управляемой системе относятся все Процессы на различных стадиях создания новой техники или продукции соответствующего качества
Каждая стадия выдвигает свои задачи, ставит свои цели и формирует факторы, влияющие на качество Продукции (рис. 15.2).
Рис. 15.2. Факторы, влияющие на формирование качества продукции
В Процессе исследования и проектирования новой техники главная задача состоит в том, чтобы повысить полезные свойства продукции в соответствии с требованиями научно-техническо прогресса и отразить их в нормативно-технической документа- ции (стандартах, чертежах и технологических картах и технически
условиях), а также предусмотреть КОМПЛеКС мероприятий по достижению заданного уровня качества Продукции.
В Процессе производства ОСНОВНОЙ задачей становится обеспечение технических, организационных, производственных и социальных условий для получения заданного уровня качества в строгом соответствии с требованиями технической документа- ции. Эта задача довольно сложная. для успешного ее решения необходимы своевременное введение прогрессивных технологических процессов и высокопроизводительного оборудования; должное обеспечение качественными материалами, инструментом и оснасткой систематическое воспитание у коллектива чувства ответственности за качество продукiIиИ; улучшение организации и повышение культуры производства; хорошая организация службы технического КОНТрОЛЯ, своевременность и достоверность информации о качестве продукции; мобилизация внимания трудовых коллективов на повышении качества продукции и культуры производства.
На стадиях реализации и эксплуатации или потребления вначале необходимо создать условия для более длительного сохранения уже полученных полезных свойств продукции в процессе ее транспортировки и эксплуатации.
Как правило, СТадИИ организационно разобшены. Исследованием И проектированием занимаются одни организации, производством и реализацией — другие, а эксплуатацией или потреблением — третьи. Между тем эффективность системы управления качеством тем и обусловливается, что формирование уровня качества продукции осуществляется в неразрывной связи всех стадий. Это выражается в постоянном оперативном обмене информацией, который позволяет управляющей системе вьщавать научно обоснованные команды управления, а также корректировать факторы, определяюшие уровень качества изделий.
15.3. организационноправовые основы систем управления качеством продукции
организационнопраВовая основа систем управления качеством базируется на Законе РФ «О стандартизапии», принятом в 1993 г. и трех государственных стандартах качества: ГОСТ 40.9001-88 «Система качества. Модель для обеспечения качества при проектировании и (или) разработке, производстве, монтаже и обслу-
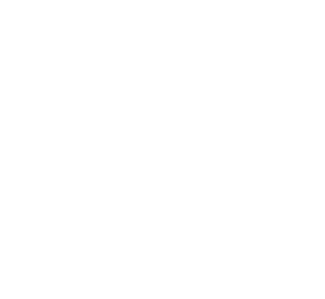
живании»; ГОСТ 40.9002-88 «Система качества. Модель для обеспечения качества при производстве и монтаже»; ГОСТ 40.9003-88 «Система качества. Модель для обеспечения качества при окончательном контроле и испытаниях».
Закон Рф «О стандартизации» устанавливает основные положения, принципы, понятия и порядок организации работ в области стандартизации, которые являются едиными и обязательными для всех органов государственного управления, субъектов хозяйственной деятельности независимо от их ведомственной принадлежности и форм собственности. Законом определены меры государственной защиты интересов потребителей, а также государства в целом посредством разработки и применения нормативных документов по стандартизации, устанавливающих оптимальньте требования к объектам стандартизации — продукции, работам и услугам, порядку осуществления государственного контроля и надзора за соблюдением обязательных требований государственных стандартов
Стандартизация — это деятельность, направленная на разработку и установление требований, норм, правил, характеристик как обязательных для выполнения, так и рекомендуемых, обеспечивающая право потребления на приобретение товаров надлежащего качества за приемлемую цену, а также право на безопасность и комфортность труда.
Цели стандартизации — достижение оптимальной степени угiорядочения в той или иной области посредством широкого и многократного использования установленных положений, требований, норм для решения реально существующих, планируемых или потенциальньх задач. Эти цели можно подразделить на общие и более узкие, касающиеся обеспечения соответствия продукции заданным требованиям. Общие цели вытекают прекце всего из содержания понятия. Конкретизация общих целей связана с выполнением трех обязательных требований стандартов.
К ним относятся разработка норм, требований и правил, обеспечивающих: безопасность продукции, работ, услуг для жизни и здоровья людей, окружающей среды и имущества; совместимость и взаимозаменяемость продукции, качество продукции, работ и услуг в соответствии с уровнем развития научно-технического прогресса; единство измерений; экономию всех видов ресурсов, основные потребительские и эксплуатационные свойства продукции, требования к упаковке, маркировке, транспортировке
хранению и утилизании техническое единство при разработке, производстве, эксплуатации продукции и оказании услуг, правила обеспечения качества продукции, сохранность и рациональное использование всех видов ресурсов, термины, определения и обозначения и другие общетехнические правила и нормы; безопасность хозяйственных объектов, связанную с воЗМОЖНОСТЬЮ возникновения различных катастроф и чрезвычайных ситуаций.
Более узкие (конкретные) цели стандартизации относятся к определенной деятельности, конкретной отрасли производства товаров и услуг, тому или иному виду продукции, системе управления и т.п.
Цели тандартиЗаЦии, установленные Законом РФ «О стандартизации», полностью соответствуют аналогичным целям стандартизации, принятым междуНародной органиЗаЫией по стандартизации (ИСО).
В процессе стандартизации разрабатываются Нормы, правила, требования и характеристики объектов стандартизации, которые оформляются в виде нормативных документов. К ним относятся: стандарты, документы технических условий, своды правил и регламенты.
Стандарт — это нормативный документ, разработанный на основе консенсуса, угнержденный признанным органом, направленный на достижение оптимальной степени упорядочения в определенной области. В стандарте устанавливаются для всеобщего и многократного использования общие принципы, правила и характеристики, ающиеСя различных видов деятельности или их результатов.
Стандарты бывают еждународнъiе, региональнЫе национальные и
Законом РФ «О тандарТизации» установлены: государственные стандарты Российской Федерации (ГОСТ Р); общероссийские классификаторы техникоэкОномичеСкой информации (ОКТЭИ) стандарты отраслей (ОСТ); стандарты предприятий (СТП); стандарты научноТехнических обществ, инженерных обществ и других 0ществеННЫх объединений (СТО).
Документ техническ условий устанавливает технические требования к продукции, услуге или процессу. Обычно в этом документе должны быть указаны Методы или процедуры, которые
241
следует использовать для проверки соблюдения требований данного нормативного документа в таких ситуациях, когда это необходимо
Свод правил, как и предыдущий нормативный документ, может быть самостоятельным стандартом либо самостоятельным документом, а также частью стандарта. Свод правил разрабатывается для процессов проектирования, монтажа оборудования и конструкций, технического обслуживания или эксплуатации объектов, конструкций, изделий Технические правила, содержащиеся в документе, носят рекомендательный характер.
Регламент — это документ, в котором содержатся обязательные правовые нормы. Регламент принимается органом власти, а не органом по стандартизации, как в случае других нормативных документов Разновидность регламентов — технический регламент — содержит технические требования к объекту стандартизации. Технические регламенты обычно дополняются методическими документами по методам контроля или проверок соответствия продукта (услуги, процесса) требованиям регламента
Государственный контроль и надзор за соблюдением обязательных требований государственных стандартов и других нормативных документов осуществляются на основании Закона РФ «О стандартизации» и составляют часть государственной системы стандартизации.
На современном этапе государственный контроль и надзор приобретает социально-экономическую ориентацию, поскольку основные его требования направлены на проверку строгого соблюдения всеми хозяйствующими субъектами обязательных норм и правил, обеспечивающих интересы и права потребителя, защиту здоровья и имущества людей и среды обитания.
Согласно Закону РФ «О стандартизации» ответственность за нарушение его положений могут нести юридические и физические лица, а также органы государственного управления Ответственность может быть уголовной, административной или гражданско-правовой.
Переход от разработки отдельных стандартов к программе комплексной стандартизации позволяет активно влиять на качество и технический уровень продукции в сфере не только ее производства на предприятии, но и эксплуатации или потребления В качестве объектов комплексной стандартизации приняты предметы производства (продукция), технические средства
стадии организании производства, стадии реализации и эксплуатации или йотребления продукции и, что особенно важно, стадия исследования и проектирования предмета производства.
На межотраслевом уровне управление качеством продукции осуществляется на основе государственных стандартов, определяющих общую терминологию по качеству, выбор показателей качества и методов их оценки, принципов построения систем управления качеством.
На отраслевом уровне управление качеством продукиии базируется на государственных и отраслевых стандартах и других нормативных документах. Последние разрабатываются для учета специфических особенностей отраслей. Отраслевьте стандарты позволяют согласовывать специфические условия организации производства и управления конкретных отраслей промышленности с требованиями государственных стандартов и другой межотраслевой научной и нормативнотехнической документации.
На уровне предприятия (объединения) управление качеством осуществляется на основе государственных и отраслевых стандартов, технических условий и стандартов предприятий и других нормативнотехнических документов. Последние отражают ори технологическую специфику работ на предприятии и условия их выполнения. Таким образом, образуется единая система, позвОляющая увязать требования к уровню качества продукции, формируемые на всех стадиях жизненного цикла изделия.
Важным моментом в повышении качества продукции, эффективности управления качеством и производством стало использование международных стандартов ИСО серии 9000 — 9004 и новых версий этих стандартов. Их содержание достаточно подробно рассмотрено в литературе [14, 15, 24].
15.4. Роль, задачи и структура органов
технического контроля и управления
качеством продукции на предприятии
Организация и проведение технического контроля качества продукции являются составными элементами системы управления качеством продукции на стадиях производства и реализации.
243
Технический контроль это проверка соответствия ПРОдуКциИ или Процесса, от которого зависит качество продукции, установ ЛеННЫм стандартам или техническим требованиям в машиНост. роении ОН представляет Собой СовокупноСть КОНТрОЛЬНЫХ операций, Выполняемых на всех стадиях Производства от контроля качества постугiающиХ на Предприятие материалов, Полуфабрика. ТОВ, комплектующих приборов и изделий до Выпуска ГОТОВОЙ Продукции. Технический контроль является неотъемлемой частью производственного процесса, он Выполняется различными службами Предприятия в зависимости от объекта контроля. Так, контроль за правильнъм использованием стандартов, техническлх условий, руководящих Материалов и другой нормативно. технической документации в Процессе технической подготовки производства осуществляет служба нормоконтроля Кроме того, качество технической документации контролируется непосредственными исполнителями и руководителями всех уровней в отделах главного конструктора главного технолога, главного меТаллурга и других служб предприятия Однако контроль качества готовой Продукции и Полуфабрикатов своего Производства осуществляет отдел технического контроля (ОТК), хотя ответственность за качество не снимается с исПолнителей и руководителей производственнъ подразделений (цехов и участков).
Основной задачей технического контроля на Предприятии является своевременное получение полной и достоверной информации о качестве продукции, состоянии Оборудования и технологического процесса с целью Предупреждения неполадок и Отклонений, которые могут привести к нарушениям стандартов и технических условий.
Технический контроль призван обеспечивать требуемую настроенность процесса производства и поддерживать его стабильность, т.е. устойчивую повторяемость каждой Операции в предусмотренных Технологических режимах, Нормах и условиях.
Объектами технического контроля на машиностроительном Предприятии ЯВЛЯЮТСЯ поступающие материалы, полуфабрикатьт на разных стадиях изготовления, готовая Продукция предприятия (детали, мелкие сборочные единицы, узлы, блоки, изделия), средства производства (оборудование инструмент, приборы, приспособления и др.), технологические процессы и режимы обработки, общая культура производства.
Функции технического контроля во многом определяются задачами и объектами производства. Это — контроль за качеством и комплектностью выпускаемых изделий, учет и анализ возвратов продукции, дефектов, брака, рекламаЦий и т. д.
Основными задачами ОТК являются предотвращение выпуска продукции, не соответствующей требованиям стандартов, технических условий, эталонов, технической документации, договорным условиям, а также укрепление производственной дисциплины и повышение ответственности всех звеньев производства за качество выпускаемой продукции.
Продукция предприятия может быть реализована только после приемки ее ОТК. При этом она должна быть оформлена соответствующим документом (сертификатом), удостоверяющим качество продукции.
В соответствии с указанными задачами ОТК выполняет следующие функции: планирование и разработку методов обеспечения качества продукции, контроль и стимулирование качества.
Планирование и разработка методов обеспечения качества включает: планирование уровня качества изделия, планирование контроля качества и технических средств контроля; сбор информации о качестве, определение затрат на обеспечение качества, обработку информации и анализ данных о качестве из сферы производства и эксплуатации; управление камеством поставляемой продукции поставщиками и управление качеством продукции на собственном предприятии разработку методик контроля, обеспечивающих сравнимость и надежность результатов контроля качества; разработку (совместно с техническими подразделениями) технических условий, кондиций и стандартов для осуществления управления качеством продукции.
Контроль качества объединяет следующие задачи: входной контроль качества сырья, ОСНОВНЫХ и вспомогательных материалов, полуфабрикатов, комплектующих изделий, инструментоВ, постугтающиХ на склады предприятия; производственный пооперационный контроль за соблюдением установленного технологического режима, а иногда и межоперационную приемку продукции; сиСтематический контроль за состоянием оборудования, машин, режущего и измерительного инструментов, контрольноизмерительных приборов, прецизионных средств измерения, штампов, моделей испытательной аппаратуры и весового хозяйства, новых и находящихся в эксплуатации приспособлений,
Условий Производства и транспортировки изделий и другие проверки; КОНТРОЛЬ моделей и Опытных образцов ГОТОВОЙ Продукции (деталей, мелких сборочных единиц, Подузлов, узлов, блоков, из- дели й).
Стимулирование качества предполагает• разработку документации, Отражающей методы и средства мотивации в области Обеспечения качества Продукции; разработку положений о премировании Работников Предприятия за качество работы (совместно с ОТделом Организации труда и заработной платы; обучение и повышение Квалификации)
Начальник Отдела технического контроля Непосредственно Подчиняется директору предприятия Он имеет право прекращать приемочный Контроль Продукции, имеющей пОВтОряющие ся дефекты, до устранения причин, Вызыватощих эти дефекты; запрещать использование сырья, материалов, Комплектующих изделий и Инструмента не Отвечающих установленным требованиям изготовления новой Продукции. При Возникновении брака начальник отк предъявляет обязательные для исполнения требования к Подразделениям и должностным лицам предприятия По устраненИЮ прИЧИI возникновения дефектов продукции и представляет Руководству Предприятия предложения о привлече нии к оГветствеi4Ности дОЛЖНОСТНЫХ ЛИЦ 14 рабочих предприятия виновных в изготовлении бракованной Продукции. Наравне с директОром и главным инженером Предприятия он несет ответственность за выпуск НедоброкачестВеныой или несоотвеТствую щей Стандартам и техническим Условиям Продукции.
Структура и Штаты ОТК предприятия разрабатываются на основе типовой Структуры с учетом задач, функций и Производственных особенностей Как Правило, в составе отдела создаются: бюро технического Контроля, территориально Размещаемые в основных и вспомогательных цехах; бюро внешней приемки, обеспечивающее входной Контроль за материалами и КОмПЛеКту ющими Изделиями; бюро заключительного контроля и испытаний готовой продукции; бюро анализа и учета брака и реклама- ции; центральная измерительная Лаборатория и ее Контрольно.. Проверочньте пункты, КОнтролирующие состояние элементов и оснастки, в том числе используемых При контроле качества; инспекторская группа, осуществляющая проверочный Контроль качества Продукции и целевые проверки Соблюдения технолоГичес.. кой дисциплины; подразделения контроля экспортной Продук246
ции; подразделение контроля качества лома и отходов цветных и благородных металлов.
Тесную связь с деятельнОстью ОТК имеют метрологический отдел; отделы стандартизации, главного технолога, главного металлурга и главного конструктора; отдел надежности; отдел или цех гарантийного обслуживания и др. Общее руководство работами по обеспечению качества продукции осуществляет главный инженер предприятия. Он привлекает для выработки и анализа вариантов управленческих решений ПОСТОЯННО действующую комиссию по качеству (ПдКК), в состав которой входят большинство главных специалистов предприятия, включая начальника ОТК. Контроль за исполнением решений этой комиссии, обработку информации по анализу и учету брака, а также расчет показателей качества труда осуществляют специалисты вычислительного центра системы управления качеством.
15.5. Сертификация продукции и систем обеспечения качества и производства
Опыт работы отечественных и зарубежных предприятий показывает; что разработка и внедрение системы управления качеством не решают проблему качества, конкурентОспособности продукции и уверенности в ее реализации. Для этого необходимо сертифицировать продукцию и систему обеспечения качества, а если это предусмотрено выбранной схемой сертификации, то сертифицировать и производство.
Термин «сертификация» в переводе с латинскОгО языка означает «сделано верно». Для того чтобы убедиться, что продукт сделан верно, надо знать, каким требованиям он должен соответствовать и как можно получить достоверные доказательства этого соответствия установленным требованиям на протяжении определенного времени. Общепризнанным способом такого доказательства служит сертификация соответствия.
Сертификация соответствия продукции — это установление СОответствия показателей (параметров) качества продукции заданным требованиям. Она связана с понятием испытания.
Под испытанием понимается техническая операция, заключающаяся в определении одного или нескольких показателей качества продукции, характеризующих ее пригодносТь удовлетворять конкретные потребности в соответствии с ее названием и
установленными требованиями. Испытания Проводятся в аккредитованных испытательных лабораториях, которые должны соответствовать требованиям ГОСТ Р 5 1000.3-96 и другим критериям.
По данным на начало 2002 г, в системе сертификации этого ГОСТа Р аккредитовано более 2000 лабораторий, из них около 350 лабораторий, занимающихся испытаниями продукции машиностроения, надзором за соответствием и обеспечением соответствия
Воспользуйтесь поиском по сайту: